НАЗНАЧЕНИЕ ПОРОШКОВЫХ СПЛАВОВ
Сплавы, изготовляемые из металлических порошков путем прессования и спекания без расплавления или с частичным расплавлением наиболее легкоплавкой составляющей их, называются порошковыми.
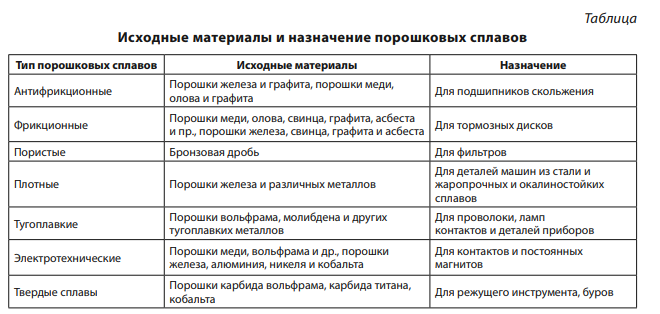
Несмотря на то, что объем производства порошковых сплавов невелик и составляет всего 0,1 % от общего объема производства металлов, они имеют весьма большое значение в производстве и экономике в целом, поскольку область их применения чрезвычайно широка. При этом изготовление многих сплавов практически возможно только из порошка, например, изготовление твердых металлокерамических сплавов, керметов, сплавов из тугоплавких металлов — вольфрам, молибден, тантал, ниобий — или композиций этих металлов с легкоплавкими металлами, или из металлов с неметаллическими материалами.
Многие детали из порошковых сплавов отличаются лучшими качествами и дешевле, чем из обычных металлов. Области применения и составы порошковых сплавов приведены в таблице.
Особенно велико значение порошковой металлургии в новых отраслях техники: атомной и химической промышленности, самолетостроении, ракетной технике, реактивных двигателях, радио- и электротехнике, энергетической промышленности и в производстве особо жаропрочных сплавов.
ПРОИЗВОДСТВО ПОРОШКОВЫХ СПЛАВОВ
Процесс производства порошковых сплавов заключается в получении порошка, составлении шихты, прессовании и спекании.
1. Производство порошков. Важнейшими методами производства порошков являются:
1) восстановление металлов из окислов;
2) механическое измельчение;
3) электролитическое осаждение;
4) распыление жидкого металла;
5) нагрев и разложение карбонилов.
Наибольшим распространением пользуются первые 2 метода.
Восстановление металлов из окислов широко применяется в производстве порошков тугоплавких редких металлов, вольфрама и молибдена, а также кобальта, никеля и железа. Руды редких металлов подвергаются сложной переработке и размолу для получения порошков окислов, которые восстанавливаются затем путем нагрева в газовой среде водородом, генераторным газом или твердыми восстановителями — сажей, коксом, графитом. Иногда применяется комбинированное восстановлена путем нагрева вместе с твердым и газовым восстановителем. Восстановление из окислов позволяет получить очень мелкие и чистые порошки.
При механическом измельчении — размоле на шаровых, молотковых и особенно на вихревых мельницах — наиболее выгодным является использование металлической стружки. Шаровые мельницы применяются для размола хрупких металлов — чугуна, закаленной стали, бронзы, окислов и др. Молотковые мельницы применяются для получения порошков алюминия и бронзы.
С 1930 г. начали широко применять вихревые мельницы, в которых измельчение производится ударами частиц металла друг о друга под действием воздушных вихрей. Вихревое дробление применяется для производства железных порошков для пористых подшипников, стальных деталей и др.
Некоторые металлы, например алюминий и магний, во избежание воспламенения измельчают в защитной атмосфере. Порошки, полученные путем механического измельчения, тверды, плохо прессуются и требуют отжига для снятия наклона.
Электролитическое осаждение применяется для производства порошков электроположительных металлов — меди и некоторых других металлов, например, титана, ванадия я других, а иногда также и железа.
Распыление жидкого металла потоком сжатого воздуха, пара или инертного газа сначала применяли для производства порошков легкоплавких металлов — алюминия, олова и свинца. В настоящее время этим методом распыляют также расплавленные сталь и чугун.
2. Испытание порошков. Порошковая металлургия предъявляет ряд требований к форме и размерам порошков. Например, для некоторых деталей требуются порошки чешуйчатой формы, полученные на вихревых мельницах, а для фильтров, наоборот, — шарообразной формы, полученные распылением. Прессуются лучше крупные порошки, особенно если среди них есть и мелкие частицы, а спекаются лучше мелкие.
Зернистость порошков определяется путем ситового анализа: порошок просеивают через ряд сит со все более мелкими отверстиями и взвешивают остатки с каждого сита. Форму зерен определяют, рассматривая их под микроскопом с сетчатым окуляром.
Насыпной вес порошка определяется весом 1 см3 свободно насыпанного порошка. Он зависит от размера, формы и состояния поверхности его частиц и является очень важной его характеристикой.
При конструировании прессформ необходимо знать насыпной вес порошка, который будет в них прессоваться, чтобы определить объем полости матрицы и ход пуансона. Перед прессованием порошки просеивают, подвергают смягчающему или восстановительному отжигу и тщательно (длительно) перемешивают.
3. Прессование. Для прессования применяют большей частью быстроходные легко автоматизируемые эксцентриковые (кривошипные) прессы, а иногда и тихоходные гидравлические прессы. Прессование производится в прессформах при давлении от 10 до 100 кг/мм2 в зависимости от твердости порошка и формы изделия: чем тверже порошок, тем больше давление прессования, при этом усадка получается от 2:1 до 6:1.
Вследствие трения порошка о стенки прессформы процесс прессования получается прерывистым, ступенчатым, нагрузка и сжатие порошка меняются скачками. Важнейшую роль при сильных давлениях прессования играет пластическая деформация частиц порошка, которая вызывает увеличение поверхности соприкосновения (контактной поверхности) их между собой. Прочность прессования объясняется двумя причинами: атомарным схватыванием на контактной поверхности — «зацеплениями», переплетением неровностей на поверхности частиц порошка.
В различных частях сечения порошок уплотняется неодинаково. При последующем спекании усадка может оказаться неоднородной, и недопрессованная часть будет плохо спекаться. Поэтому прессование проходит лучше при наличии деталей небольшой высоты. Вместе с тем порошок не может, подобно жидкости, заполнить очень сложную фасонную форму. Следовательно, из порошковых сплавов можно изготовлять детали сравнительно не очень сложной формы.
4. Спекание. Для спекания порошковых сплавов применяют электропечи с металлическим сопротивлением, с угольными сопротивлениями в виде труб и высокочастотные. Спекание производится в защитной атмосфере. Для спекания медных сплавов, железа и фрикционных материалов применяют защитные атмосферы, получаемые при частичном сжигании газа.
При спекании вольфрама, молибдена, твердых сплавов, магнитных и электротехнических материалов применяют водород. Температура спекания составляет примерно 2/3 температуры плавления металла, например для меди 800–850 °С, для железа — 1050–1150 °С. Длительность спекания составляет примерно 2–3 ч.
Различаются 2 основных типа спекания:
• спекание однокомпонентной системы;
• спекание многокомпонентной системы с образованием или без образования жидкой фазы.
При спекании происходят следующие процессы:
• повышение температуры увеличивает подвижность атомов;
• изменение контактной поверхности частиц, которая большей частью увеличивается;
• снятие напряжений в местах контакта и рекристаллизация, сопровождающаяся ростом зерна через контактные поверхности;
• восстанавливаются окислы и удаляются адсорбированные газы и жидкости, в результате контакт становится металлическим.
В случае многокомпонентных систем, кроме перечисленных явлений, происходит образование твердых растворов, диффузия и образование химических соединений.
При спекании порошков с большой разницей температур плавления, например порошков карбида вольфрама с порошком кобальта, образуется жидкая фаза, которая капиллярными силами стягивает нерасплавившиеся частицы. В результате получаются плотные детали.
Иногда, например при производстве медновольфрамовых электродов, сначала прессуют и спекают порошковый вольфрамовый каркас, потом пропитывают его расплавленной медью.
Спекание обычно сопровождается усадкой, которая тем больше, чем выше температура спекания и чем ниже давление прессования. Усадка изменяет размеры деталей. Поэтому детали, требующие высокой точности, например подшипники и зубчатые колеса, после спекания калибруют путем протягивания через сквозные прессформы.
У сплавов, образующих жидкую фазу, усадка и процессе спекания составляет 5–25 %, а у сплавов, не образующих жидкой фазы, усадка составляет 0,5–2,5 %.
Горячее прессование, совмещающее прессование и спекание, благодаря ряду преимуществ, распространяется все шире. При горячем прессовании требуется более низкое давление, которое составляет всего 5–10 % давления обычного прессования. Порошок при этом лучше заполняет форму, поэтому горячее прессование позволяет получать детали более сложной формы и более точных размеров, не требующих калибрования. Нагрев порошка производится электрическим током.
ТВЕРДЫЕ ПОРОШКОВЫЕ СПЛАВЫ
1. Классификация. Порошковым твердым сплавом является сплав, состоящий из тончайших частиц (зерен) карбидов, например WC, связанных твердым раствором WC в кобальте. Существуют 2 основные группы металлокерамических (порошковых) твердых сплавов — вольфрамовые, состоящие из карбида вольфрама и кобальта, и титановольфрамовые, состоящие из карбида титана, карбида вольфрама и кобальта.
Металлокерамические или порошковые твердые сплавы применяются при изготовлении пластинок для оснастки инструмента при обработке металлов резанием, волок при волочении проволоки, бурового инструмента и других целей, в том числе для износоустойчивых деталей (клапанов насосов, работающих в коррозионной среде, наконечников пескоструйных аппаратов, разных направляющих) и измерительного инструмента.
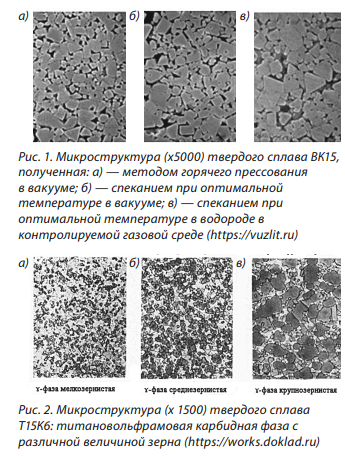
2. Микроструктура. Качество и режущие свойства твердых порошковых сплавов зависят от их микроструктуры. Исследование их микроструктуры до травления обнаруживает пористость (рис. 1).
Микроструктура вольфрамокобальтового твердого сплава ВК15 после травления насыщенным солянокислым раствором хлорного железа обнаруживает следующие 2 фазы:
• светлые угловатые и шпалообразные зерна фазы WC;
• протравленные в темный цвет участки фазы твердого раствора WC в кобальте.
Светлые зерна WC являются очень твердыми, в режущем инструменте они служат элементарными режущими частичками, а твердый раствор WC в кобальте — относительно менее твердый, но более вязкий служит связкой (цементом), соединяющей между собой зерна WC.
Твердый раствор WC в кобальте лучше протравливается легким окислением на воздухе в электрической печи при 400 °С в течение 10 мин., но очертания WC выявляются здесь менее четко.
Важно отметить, что чем мельче частички (зерна) и чем равномернее они распределены в микроструктуре, тем лучше режущие свойства и тем выше прочность металлокерамического (порошкового) вольфрамового твердого сплава данной марки. Крупные же зерна WC ухудшают свойства этих сплавов.
Микроструктура титановольфрамокобальтового сплава Т15K6 после травления окислением на воздухе в электропечи при 400 °С в течение 40 мин. состоит из 3-х фаз (рис. 2, а): угловатых светлых зерен фазы WC, окаймленных темной фазой (твердого раствора карбидов WC и TiС в кобальте и серой титановой фазы), твердого раствора WC в TiC.
Карбид вольфрама WC почти не растворяет титана, зато карбид титана TiC растворяет очень много вольфрама, например, до 70 % при комнатной температуре и до 90 % при высокой температуре.
Чем мельче и равномернее распределены светлые зерна фазы WC (рис. 2, б), тем лучше режущие свойства и прочность твердого сплава Т15К6. Зерна титановой фазы имеют округлую форму (рис. 2, в). Они выявляются путем травления в щелочном растворе K4Fe(CN)6. Хорошим режущим свойствам сплава Т15К6 отвечает микроструктура из средних или крупных зерен титановой фазы.
Избыток углерода в порошковых твердых сплавах вызывает появление в их микроструктуре графита, а при недостатке углерода образуется n1-фаза (W4Co4C).
Присутствие графита, n1-фазы и других посторонних включений в микроструктуре порошковых твердых сплавов ухудшает их качество.
Механические и физические свойства. Предел прочности на изгиб и твердость порошкового твердого сплава зависят от содержания в нем кобальта. Чем больше в твердом сплаве кобальта и чем крупнее зерна карбидов, тем выше предел прочности на изгиб, но тем ниже твердость. Однако повышение содержания кобальта сверх 15 % нарушает сплошной каркас из зерен карбида и резко снижает предел прочности на изгиб.
В случае уменьшения содержания кобальта и применения мелкозернистых карбидов, которые лучше растворяются в кобальте, вязкость и предел прочности на изгиб снижаются, но твердость и износостойкость увеличиваются.
Удельный вес характеризует степень пористости сплава. Высокая теплопроводность способствует отводу тепла от режущей кромки и увеличивает стойкость инструмента.
Красностойкость твердых сплавов, т. е. способность сохранять структуру и режущие свойства при высоких температурах, значительно выше красностойкости быстрорежущей стали. При этом чем меньше кобальта в сплаве и чем он мелкозернистее, тем выше красностойкость.
Титановольфрамовые сплавы обладают большей красностойкостью, чем однокарбидные вольфрамовые, что особенно важно при обработке стали. Кроме того, наличие карбида титана снижает коэффициент трения и увеличивает износостойкость двукарбидных сплавов.
Слипаемость или сцепление твердого сплава с обрабатываемым материалом резко ухудшает обрабатываемость, особенно стальных деталей.
Твердые титановольфрамовые сплавы группы ТК отличаются меньшей слипаемостью, которая начинается у них при более высоких температурах, чем у вольфрамовых ВК. Кроме того, чем меньше в твердом сплаве кобальта, тем меньше слипаемость.