В результате внедрения производственных систем на предприятиях, которыми мне приходилось руководить, формировалась культура постоянных улучшений, охватывающая все стороны бизнеса, когда каждый сотрудник нацелен на поддержание стандартов и постоянное улучшение бизнес-процессов, и удавалось добиться повышения производительности в среднем до 5 % каждый год. В компании ESAB, например, благодаря внедренной производственной системе, себестоимость продукции (сварочные электроды и сварочный флюс) удерживалась на одном уровне в период с 2008 по 2014 г., несмотря на ежегодную инфляцию в 10 %.
Ключевая роль в достижении наиболее высокого показателя поставки вовремя и в полном объеме (OTIF), несомненно, принадлежит производственной структуре. Достижение наивысшего значения показателя OTIF определяется тем, насколько слаженно организована работа всех частей сложного производственного организма.
Последние 6 лет я руковожу производственным предприятием в Эстонии. Предприятие входит в международную корпорацию JELD-WEN, занимается обработкой древесины сосны и производит 10 тыс. панельных дверей и 160 тыс. комплектов дверных рам в месяц. За три года на предприятии была внедрена производственная система, обеспечившая постоянное совершенствование процессов и постепенное улучшение достигаемых результатов в области безопасности, качества и производительности. Благодаря совершенствованию производственной системы нам удалось существенно улучшить показатели. Например, в сфере безопасности — на момент написания статьи в течение 440 дней не было ни одной травмы. В области качества — благодаря системе постоянного совершенствования технологических процессов брак снизился на 40 %. В области дисциплины поставок — время поставки сократилось на 30 %, а процент заказов, поставленных покупателю вовремя и в полном объеме, вырос с 80 до 98 %. В результате производительность повышалась в среднем на 5 % ежегодно.
ДОСЬЕ
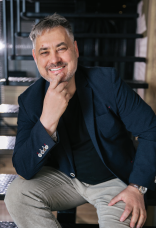
Олег Лавренов — директор завода компании JELD-WEN Eesti AS, Республика Эстония.
А втор собственной методик и внедрения системы управления безопасным поведением и формирования культуры безопасного поведения на производстве.
Более 20 лет управляет производственными предприятиями в составе крупных международных компаний, в т. ч.: Ariston Thermo Group (2003–2008 гг.), ESAB (2008–2016 гг.), Jeld-Wen (2016 г. — по н. в.). На всех предприятиях руководил построением и развитием производственных систем постоянного совершенствования, которые обеспечили существенное улучшение показателей компаний в области безопасности, качества и производительности.
В 2006 г. завод полного цикла Ariston Thermo Group в России был признан л у чшим предпри ятием группы «Аристон» в мире, награжден Quality Grand Prix.
В 2020 г. завод компании JELD-WEN Eesti AS в Эстонии был удостоен награды президента компании Operational Excellence CEO Award, как лучшее производственное предприятие группы. Разработанная и внедренная Олегом Лавреновым система, обеспечивающая безопасное поведение на производстве, принята к внедрению на 12 предприятиях группы в Северной Европе — в Финляндии, Швеции, Дании, Латвии, Эстонии.
Что нужно сделать компаниям, решившим встать на путь внедрения системы постоянного совершенствования? Какие первые шаги необходимо сделать?
Рекомендации основаны на практическом опыте автора по внедрению производс твенных сис тем в международных производственных компаниях.
Первое, что необходимо сделать, — собственники и руководители бизнеса должны на уровне ценностей компании заявить о том, что постоянное совершенствование является образом жизни каждого сотрудника компании. Одновременно с заявлением принять решения о внедрении производственной системы, постановке целей, определении задач, сроков и показателей, выделении ресурсов, назначении управляющего комитета и распределении ответственности.
В результате внедрения производственных систем на предприятиях формировалась культура постоянных улучшений, охватывающая все стороны бизнеса, когда каждый сотрудник нацелен на поддержание стандартов и постоянное улучшение бизнес-процессов, и удавалось добиться повышения производительности в среднем до 5% каждый год.
Второй шаг — следует провести обучение основам производственной системы на уровне менеджеров, специалистов и мастеров с целью формирования активного ядра сторонников изменений.
Правильно построенная и функционирующая Производственная Система обеспечивает эффективное выявление потерь и структурированное решение проблем, связанных с этими проблемами. Производственная Система — это дом, который под одной крышей объединяет взаимосвязанные строительные блоки. Как и в доме, строительные блоки производственной системы соединены связующим раствором. Связующий раствор состоит из двух компонентов. Первый компонент — это принятие того факта, что истинной ценностью бизнеса является только то, что имеет ценность для клиента: то, за что клиент готов платить, все остальное есть потери, с которыми бизнесу предстоит бороться. Второй компонент — это принятие философии постоянного улучшения, двигателем которой служит знаменитый цикл Деминга: Планируй — Делай — Проверяй — Воздействуй (Plan-Do-Check-Act).
Третий шаг — это монтаж строительных блоков.
Первым по важности для внедрения строительным блоком производственной системы служит комплекс инструментов для визуализации хода выполнения бизнес-процессов. Во всех компаниях, где я руководил внедрением производственных систем, инструментом визуализации служили информационные доски, на которых в стандартизированной форме отображается регулярно обновляемая информация о текущем состоянии и ходе бизнес-процессов. Процессы группируются в области деятельности и отображаются в порядке их приоритетности для бизнеса, но, как правило, в таком порядке: Люди — Безопасность — Качество — Поставка — Затраты — Запасы — Техобслуживание.
Для каждой области деятельности применяется стандартная логика подачи информации — реализуется принцип постоянного улучшения — цикл Деминга. Установленные ключевые показатели деятельности представляются в виде Целевого показателя (Планируй) — Фактического показателя (Делай) — Отклонения (Проверяй). Например, для области деятельности «Поставка» используются описанные выше показатели: время поставки (Lead-Time), процент поставки вовремя и в полном объеме (OTIF) и количество и стоимость непоставленной задолженности — PD (Past Dues). При отклонении показателя от цели выше допустимого запускается процесс Базового Решения Проблем (Воздействуй). Обновление информации производится в зависимости от вида и сути рассматриваемых процессов и может варьироваться от почасового до еженедельного. Информационные доски размещаются в каждом подразделении в месте, удобном для проведения командных совещаний «на ногах». Совещания проводятся регулярно, мы проводим их ежедневно, в установленное время.
В моей пос ледней компании во время пандемии коронавируса мы столкнулись с ограничениями на проведение совещаний, требующих личного присутствия участников. Сначала мы растерялись, но выход быстро был найден — наши «айтишники» в короткий срок освоили программу MS Power BI, оказавшуюся мощным инструментом сбора, анализа и визуализации данных. Каждое утро программа формирует стандартные формы графических отчетов по каждому направлению деятельности. Совещания «на ногах» во время пандемии тоже переместились в онлайн, в MS Teams. Мы нашли много плюсов в формате онлайн-совещаний — строгий график, неограниченное число участников, возможность записи и ведения лога. Во время совещания каждый ответственный за область деятельности менеджер с помощью стандартных графических отчетов информирует команду о текущем состоянии своих процессов и их ключевых показателей. При отклонении какого-либо показателя от целевого значения ответственный менеджер сообщает о коренной причине, вызвавшей отклонение, и корректирующих действиях, ответственных за действия, и сроках их реализации, а также о необходимой помощи со стороны членов команды с целью скорейшего решения проблемы.

Правильно построенная и функционирующая Производственная Система обеспечивает эффективное выявление потерь и структурированное решение проблем, связанных с этими проблемами.
Приведу пример визуализации одного из основных бизнес-процессов, а именно процесса Поставки (Delivery). Визуализация бизнес-процесса Поставки позволяет вывести из функциональной изоляции и объединить в один процесс и одну цель действия нескольких подразделений компании: коммерческой службы, службы планирования и логистики, службы управления персоналом, службы обеспечения производства и само производство. Выстраивание в один процесс подразделений, исторически являющихся функционально изолированными, становится критически важным для операционной эффективности компании во время кризиса. Визуализация и постоянное совершенствование процесса Поставки позволяет предложить покупателям сервис премиум-уровня, удерживать существующих и привлекать новых клиентов, сокращать внутренние издержки, обеспечивая рост прибыли бизнеса.
Обычно функционально изолированные коммерческая служба и службы производства действуют в противоположных направлениях, так как имеют разные цели. Мне часто приходилось сталкиваться с ситуацией, когда служба продаж хочет получить как можно более широкий ассортимент в как можно меньших объемах, а производство в свою очередь, наоборот, заинтересовано в как можно более крупных партиях и ограниченном ассортименте. Часто стремление коммерческой службы иметь в своем распоряжении широкий ассортимент товара в небольших объемах бывает продиктовано не реальным спросом, а вызвано стремлением получить его, что называется «на всякий случай, вдруг понадобится». Однако опыт подсказывает, что в большинстве случаев не понадобится, но это приведет, с одной стороны, к росту невостребованных запасов, а с другой — к замораживанию оборотных средств и, как следствие, к снижению финансовой устойчивости компании. Причем двойной ущерб будет нанесен, когда запасы будут признаны обсолетами, которые придется списать в затраты текущего периода при следующей инвентаризации, а потом еще и заплатить за их утилизацию. Для производственной части компании подобная ситуация также имеет отрицательные эффекты. Помимо прямых потерь ресурсов, затраченных на производство невостребованной продукции, само производство этой продукции в большом ассортименте и в небольших объемах приводит к росту общей себестоимости продукции, так как требует более частых переналадок и связанных с ними дополнительных потерь прямых и косвенных материалов и производственной мощности.
Для визуализации хода процесса Поставки мы выбрали следующие показатели эффективности (KPI — Key Performance Indicators). Время поставки — LT (Lead-Time), процент заказов, поставленных покупателю вовремя и в полном объеме — OTIF (On-TimeIn-Full), количество и стоимость непоставленной задолженности — PD (Past Dues).
Показатель времени поставки LT выражается в днях и отображает время, проходящее от размещения заказа на поставку до получения товара покупателем. Полное время поставки складывается из времени обработки и планирования производства поступившего заказа, включая заказ материалов и планирование производственной мощности, времени самого производственного процесса, а также времени отгрузки и доставки покупателю. Мы взяли за цель значение этого показателя исходя из запроса клиентов и развернули работу по улучшению всех слагаемых, чтобы достичь требуемого показателя. В результате нам удалось превзойти требуемое время поставки, сократив его с более чем 30 до 17 дней по основным группам продуктов.
Первым по важности для внедрения строительным блоком производственной системы служит комплекс инструментов для визуализации хода выполнения бизнес-процессов.
Показатель поставки вовремя и в полном объеме (OTIF) выражается в процентах и отображает соотношение количества фактически поставленного точно вовремя товара и заказанного к поставке на требуемую дату. OTIF показывает, насколько бизнес способен выполнять взятые перед покупателем обязательства по объему и дате поставки. По причине меняющихся внешних факторов не всегда возможно обеспечить 100 %-е выполнение, поэтому обычно от 95 до 98,5 % принимается как хороший показатель. Конечно, существуют особые случаи и особые покупатели, когда требуется 100 %-е выполнение, в таких случаях необходимо производить приоритезацию. Но если бизнес сможет предложить стабильное и постоянное достижение 100 %-й поставки вовремя и в полном объеме, то, без сомнения, это будет соответствовать самым лучшим ожиданиям покупателей и обеспечит бизнесу долгосрочное конкурентное преимущество в глазах его клиентов.
Ключевая роль в достижении наиболее высокого показателя поставки вовремя и в полном объеме, несомненно, принадлежит производственной структуре. Здесь мы затрагиваем очень глубокую и сложную тему, потому что достижение наивысшего значения показателя OTIF определяется тем, насколько слаженно организована работа всех частей сложного производственного организма. Любое производственное предприятие работает в 4М системе координат — Люди, Оборудование, Материалы, Процессы (Men, Machines, Materials, Methods). Сбой в работе любой из этих составляющих немедленно ставит под угрозу выполнение задачи поставки вовремя и в полном объеме. Люди должны быть наняты в достаточном количестве, чтобы управлять оборудованием, транспортом и выполнять ручные работы, необходимые по процессу. Они должны быть обучены безопасным методам работы, безопасному поведению и стандартным операциям по выполнению процессов, в которых они задействованы. Оборудование должно быть исправным, чистым, смазанным и готовым к работе. Запасные части для критического оборудования и расходные материалы должны быть в необходимом количестве и быть доступны. Материалы должны быть требуемого качества и в необходимом количестве. Процессы должны быть регламентированы и разбиты на стандартные операции, которым должны быть обучены люди (см. выше). Параметры процессов и максимально допустимые отклонения от их средних значений должны быть определены, а контроль за ними должен быть встроен в сам процесс и возложен на тех, кто в этом процессе непосредственно участвует, с помощью тех же стандартных операций.
Визуализация хода бизнес-процессов и ежедневное совещание «на ногах» имеет мощное командо-формирующее действие — все члены команды одинаково представляют текущую картину по каждому направлению, формируется одинаковое понимание, где сейчас наиболее сложная ситуация, какие действия предпринимаются, где требуется сфокусировать больше командных усилий, какие для этого выделены сроки и кто является ответственным за реализацию контрмер.
Визуализация хода бизнес-процессов и ежедневное совещание «на ногах» имеет мощное командо-формирующее действие — все члены команды одинаково представляют текущую картину по каждому направлению, формируется одинаковое понимание, где сейчас наиболее сложная ситуация, какие действия предпринимаются, где требуется сфокусировать больше командных усилий, какие для этого выделены сроки и кто является ответственным за реализацию контрмер.
Вторым по важности для внедрения строительным блоком производственной системы служит комплекс инструментов Базового Решения Проблем. Внедрение и широкое использование этих инструментов жизненно необходимо для того, чтобы решались именно коренные причины проблем и сами проблемы никогда не повторялись. Если в вашем бизнесе проблемы в различных областях деятельности не решаются, а приходят снова и снова, то это значит только одно — вы не знаете, что является коренной причиной, источником вашей проблемы, и работаете со следствиями. Иными словами, вы не лечите заболевание, а устраняете симптомы, лежащие на поверхности, а заболевание тем временем продолжается, и рецидивы происходят снова.
Если в вашем бизнесе проблемы в различных областях деятельности не решаются, а приходят снова и снова, то это значит только одно — вы не знаете, что является коренной причиной, источником вашей проблемы, и работаете со следствиями. Иными словами, вы не лечите заболевание, а устраняете симптомы, лежащие на поверхности.
Основным и, на мой взгляд, самым мощным инструментом в комплексе Базового Решения Проблем является инструмент 5 Почему (5 Whys). Доказано, что в ситуациях, когда нет необходимости собирать и анализировать большие объемы сложных данных, для определения коренной причины проблемы достаточно пять раз (иногда достаточно трех) задать вопрос «Почему»? Например, в моем опыте, в самом начале внедрения производственной системы на моем предприятии, был такой случай — мы проводили утреннее совещание «на ногах» у информационной доски уровня завода. Менеджер по техническому обслуживанию делал сообщение по изменению показателей в своей зоне ответственности и сказал, что за прошедшие сутки случился простой покрасочной линии, причиной простоя был разрыв ленты конвейера из-за заклинивания ролика. Ролик был заменен, после чего работа линии была восстановлена. Простой составил 1,5 часа, и поэтому выпуск готовой продукции тоже оказался меньше планируемого. В результате простоя произошло увеличение времени производственного цикла и, как следствие, времени поставки LT, снизился процент поставки вовремя и в полном объеме OTIF и увеличилась задолженность по поставке PD — тем самым снизив удовлетворенность покупателя. Если бы мы остановились на этом и не пошли по пути «5 Почему?», выясняя коренную причину проблемы, то она не была бы решена на системном уровне и через какое-то время вернулась бы снова, вызвав очередную неудовлетворенность покупателя сбоем в поставке. Пройдя по пути выявления коренной причины, мы выяснили, что заклинивание ролика произошло из-за загрязнения поверхности (первый раз «Почему?»), поверхность загрязнена, потому что эта часть линии не была очищена оператором (второй раз «Почему?»), поверхность не была очищена оператором, потому что отсутствует процедура очистки этой части линии в стандартной операции оператора (третий раз «Почему?»). Таким образом мы выяснили, что коренной причиной простоя является отсутствие процедуры очистки части линии в стандартной операции оператором, и, следовательно, корректирующими действиями были корректировка стандартной операции, включение в нее процедуры очистки и обучение оператора.
В дополнение к этим двум, описанным выше, примерам основных строительных блоков производственной системы постоянного совершенствования существует еще ряд основных строительных блоков, внедрение которых обязательно для создания производственной культуры, соответствующей международному уровню. Эти блоки — Стандартная работа (Standard Work), Организация и безопасность на рабочих местах (5S), Многоуровневый аудит (MLA — Multi-Layer Audit).
В результате внедрения производственной системы на моем предприятии мы сформировали культуру постоянного улучшения, когда каждый сотрудник нацелен на поддержание стандартов и постоянное улучшение процессов с помощью инструментов Базового Решения Проблем. Как итог мы получили стандартные процессы с минимальными отклонениями параметров, обеспечивающие низкий процент брака (брак снизился с 10 до 5 %) и высокий выход годной продукции стандартного качества. Внедрение производственной системы позволило повысить удовлетворенность клиентов, сократив время поставки LT с 30 до 15 дней и подняв процент поставок вовремя и в полном объеме OTIF с 80 до 99 %. Существенное улучшение дисциплины поставок позволило покупателям снизить буферные запасы на своей стороне и высвободить замороженные денежные средства. Собственные затраты были также поставлены под контроль, а с помощью инструментов производственной системы и ее циклов постоянного улучшения мы добились улучшения производительности с 3 до 5 % ежегодно.
В условиях санкций, когда ряд международных производственных компаний уходит из нашей страны, очень важно не только сохранить производственную культуру международного уровня, но и массово создавать ее в тех производственных компаниях, которые только ищут свой путь. Первыми в новых условиях будут те, кто не станет ждать, а засучив рукава займется трансформацией своих бизнесов. Основой такой трансформации является производственная система, построенная на принципе постоянного улучшения, охватывающая все сферы бизнеса и позволяющая постоянно учиться и находить новые способы лучше удовлетворять клиентов и самим компаниям быть прибыльным и стабильным бизнесом для собственников и работников.
Для каждой области деятельности применяется стандартная логика подачи информации — реализуется принцип постоянного улучшения — цикл Деминга. Установленные ключевые показатели деятельности представляются в виде Целевого показателя (Планируй) — Фактического показателя (Делай) — Отклонения (Проверяй).