СОЗДАНИЕ ОТВЕРСТИЙ ПОСРЕДСТВОМ ЭЛЕКТРОННО-ЛУЧЕВОЙ ОБРАБОТКИ
Термическая размерная обработка металла посредством электронно-лучевой обработки (ЭЛО), как правило, предназначена для изменения его химического состава или структуры, получения отверстий заданного диаметра или пазов заданной ширины, глубины и профиля сечения.
Результат размерной обработки зависит от поведения материала при повышении температуры, в результате чего происходят следующие явления:
• фазовые превращения в твердом состоянии, появляющиеся, например, при закалке соответствующих сталей;
• сублимация — удаление материала при выполнении отверстий, пазов, резании, гравировании (алмаза, графита, кварцевого стекла);
• разложение твердого материала на летучие компоненты и унос материала при резании (синтетические материалы, керамика и др.);
• разложение с образованием, по крайней мере, одного твердого компонента и удаление материала при резании, сверлении, гравировании арсенида галлия, фосфида галлия;
• плавление материалов — микросварка, полирование металлов и полупроводниковых материалов (кремний, германий), нанесение рисок оплавлением (кремний, германий, керамика, ферриты), легирование полупроводников путем вплавления лигатур при изготовлении полупроводниковых приборов и интегральных микросхем;
• испарение — удаление материала при сверлении, резании, гравировании металлов, диэлектриков, синтетических материалов.
Обрабатываемость материала в основном зависит от его теплофизических свойств и удельной мощности пучка электронов. Чтобы избежать избытка жидкой фазы, добиться максимальной производительности за счет реализации резонансных режимов нагрева, обработку ведут в импульсных режимах. При этом возможны следующие технические варианты обработки: моноимпульсная, многоимпульсная, с быстрым отклонением луча.
В процессе электронно-лучевой обработки металлов происходит выброс жидкой фазы. Экспериментальные данные различных исследователей по измерению удельной работы разрушения показывают, что практически для всех металлов превалирует энергия плавления в сравнении с энергией превращения в пар. В продуктах выброса находится значительное количество жидкой фазы. Затраты введенной энергии, приводящие к удалению вещества при обработке и при сварке с «кинжальным» проплавлением, например, сталей, только на 10–20 % превышают затраты на плавление. Это приводит к малому различию в энергетических балансах процессов получения отверстий и проплавления, и существенно упрощает их тепловые расчеты.
Причины преждевременного вскипания вещества, приводящего к выносу жидкой фазы, в основном, можно свести к двум моментам:
• за счет гетерогенных центров зарождения паровой фазы;
• вследствие перегрева.
В первом случае факторами, облегчающими вскипание, являются:
• пузырьки растворенного в металле газа, объем которого может превышать объем основного металла в десятки и даже сотни раз;
• неидеальность контактов;
• локальные пульсации температуры, например, вследствие неоднородности временной структуры импульса энергии, приводящие к генерации внутрь материала волн сжатия и разрежения, как и при ультразвуковых колебаниях.
Объяснить причины вскипания при перегреве затруднительно из-за сложности физики процесса. Перегрев может возникать вследствие того, что нагрев и плавление металла в зоне действия луча происходят в условиях сжатия материала давлением отдачи паров. Так как разгрузка в расплавленном объеме после прекращения действия импульса энергии происходит за время ~103 –104 с, т. е. со скоростью распространения волн напряжения (скорость звука), то металл практически мгновенно заметно перегревается, что равносильно быстрому избыточному тепловыделению в локальном объеме.
Согласно другой точке зрения, перегрев связан с наличием в зоне действия луча 2-х слоев с разным характерным временем изменения температуры. Если при колебаниях интенсивности нагрева внутренние слои жидкой фазы попадают в условия перегрева, то происходит вскипание, так как одновременно является временем релаксации давления отдачи.
Вскипание и вынос жидкой фазы могут быть связаны с периодическими (вследствие экранировки) колебаниями давления отдачи паров при поверхностном испарении, которые приводят к генерации в жидком объеме металла механических колебаний, стимулирующих рост равновесных пузырьков растворенного газа.
СВАРКА МЕТАЛЛОВ ЭЛЕКТРОННЫМ ЛУЧОМ
Электронно-лучевая сварка (ЭЛС) металлов основана на использовании для нагрева энергии электронного луча.
Сущность данного процесса состоит в использовании кинетической энергии электронов, движущихся в высоком вакууме с большой скоростью.
При бомбардировке электронами поверхности металла подавляющая часть кинетической энергии электронов превращается в теплоту, которая используется для его расплавления.
Для сварки металла необходимо получить свободные электроны, сконцентрировать их и сообщить им большую скорость с целью увеличения их энергии, которая в свариваемом металле должна превратиться в теплоту при торможении. Получение свободных электронов достигается применением раскаленного металлического катода, эмитирующего (испускающего) электроны. Ускорение электронов обеспечивается электрическим полем с высокой разностью потенциалов между катодом и анодом.
Фокусировка — концентрация электронов — достигается использованием кольцевых магнитных полей. Резкое торможение электронного потока происходит автоматически при внедрении электронов в металл. Электронный луч, используемый для сварки, создается в специальном приборе — электронной пушке.
Электронная пушка представляет собой устройство, с помощью которого получают узкие электронные пучки с большой плотностью энергии (рис. 1 и 2).
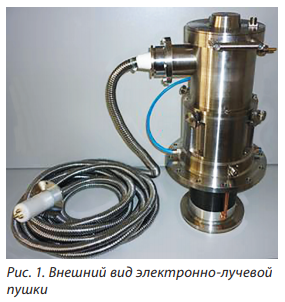
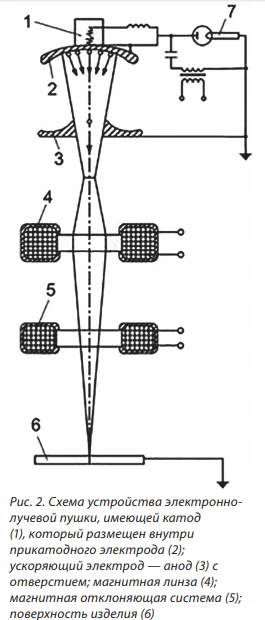
Прикатодный и ускоряющий электроды имеют форму, обеспечивающую такое строение электрического поля между ними, которое фокусирует электроны в пучок с диаметром, равным диаметру отверстия в аноде. Положительный потенциал ускоряющего электрода может достигать нескольких десятков тысяч вольт, поэтому электроды, эмитированные катодом, на пути к аноду приобретают значительную скорость и, соответственно, кинетическую энергию.
После ускоряющего электрода электроны движутся равномерно. Питание пушки электрической энергией осуществляется от высоковольтного источника постоянного тока. Электроны имеют одинаковый заряд, поэтому они отталкиваются друг от друга, вследствие чего диаметр пучка увеличивается, а плотность энергии в пучке уменьшается.
На некотором удалении от катода находится ускоряющий электрод — анод (3) с отверстием (рис. 2). Для увеличения плотности энергии в луче после выхода электродов из анода электроны фокусируются магнитным полем в специальной магнитной линзе (4). Сфокусированные в плотный пучок летящие электроны ударяются с большой скоростью о поверхность изделия (6), при этом кинетическая энергия электронов, вследствие торможения в веществе, превращается в теплоту, нагревая металл до высоких температур.
Для перемещения луча по свариваемому изделию на пути электронов помещают магнитную отклоняющую систему (5), позволяющую направлять электронный луч точно по сварочному стыку.
Для обеспечения беспрепятственного движения электронов от катода к аноду и далее к изделию, для тепловой и химической изоляции катода, а также для предотвращения возможности дугового разряда между электродами в установке создается высокий вакуум порядка 1,3 · 10–2 Па (~1 · 10–4 мм рт. ст.), обеспечиваемый вакуумной системой установки.
Работа, затраченная электрическим полем на перемещение заряда из одной точки в другую, равна произведению величины заряда на разность потенциалов между этими двумя точками. Эта работа затрачивается на сообщение электрону кинетической энергии.
Таким образом. энергия электронов может достигать больших значений и зависит от разности потенциалов разгоняющего поля. В настоящее время наиболее широко используются электронно-лучевые установки с ускоряющим напряжением в электронно-лучевой пушке до 200 кВ.
Физическая картина внешних явлений, сопровождающих действие электронов на металл, состоит из рентгеновского излучения, теплоизлучения, возникновения отраженных, вторичных электронов, испарения металла в виде атомов и ионов металла. Схема данных явлений изображена на рис. 3.
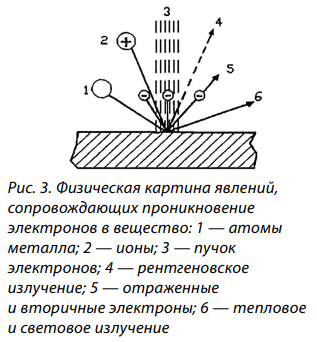
Вторичные электроны делятся на 3 группы: упруго отраженные электроны, энергия которых примерно равна падающим; электроны, отраженные в результате неупругого соударения и имеющие более или менее большие потери; собственно вторичные электроны, энергия которых не превышает 50 эВ.
Характерные значения параметров сварочных электронных лучей:
• минимальный радиус пучков — 0,1–1 мм;
• энергия - 10–200 кэВ;
• мощность — до 120 кВт.
Плотность энергии в источнике нагрева является одной из основных характеристик источника и определяет его эффективный коэффициент использования тепла, форму провара, размеры зоны термического влияния, сварочные деформации и поводки.
Электронный луч — наиболее эффективный источник нагрева металла при сварке, поскольку плотность энергии в луче превышает плотность энергии электрической сварочной дуги более чем на 3 порядка.
Ниже в таблице приведены сравнительные данные по максимальной плотности энергии и минимальной площади пятна нагрева для различных видов сварки.
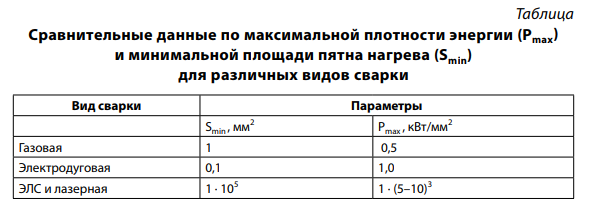
При сварке электронным пучком формируется узкий и глубокий шов. Глубина проплавления достигает 200...400 мм, а отношение глубины проплавления к средней ширине шва составляет 20...30 (рис. 4).
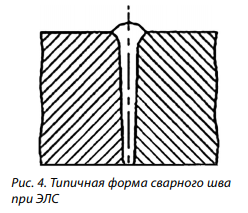
Столь глубокое проникновение электронов в металл объясняется образованием канала в сварочной ванне практически на всю ее глубину. Основным фактором, вызывающим образование канала в жидком металле, является давление отдачи пара при испарении. В связи с этим канал в сварочной ванне часто называют пародинамическим.
ПРЕИМУЩЕСТВА И НЕДОСТАТКИ ЭЛС
Технологические возможности и преимущества электронно-лучевой сварки состоят в следующем:
а) при ЭЛС возможно соединение за один проход металлов и сплавов толщиной в наиболее широком среди других методов сварки диапазоне от 0,1 до 400 мм;
б) благодаря высокой концентрации энергии в луче, минимальному вводу тепла и высокой скорости охлаждения зона термического влияния при ЭЛС имеет существенно меньшую протяженность, а снижение свойств в ней относительно небольшое. Особое значение это имеет для аустенитной стали, сплавов циркония, молибдена и других металлов, склонных при нагреве к значительному росту зерна и снижению коррозионной стойкости;
в) глубокое проплавление металла при малой погонной энергии обусловливает значительно большую скорость отвода тепла от зоны сварки, что обеспечивает увеличение скорости кристаллизации малой по объему сварочной ванны с получением мелкокристаллического строения металла шва, по своим свойствам мало отличающегося от основного металла;
г) ввод значительно меньшего количества тепла при ЭЛС, особенно на импульсном режиме, в сравнении с дуговой сваркой дает возможность заметно уменьшить деформацию свариваемых изделий;
д) большая концентрация энергии в малом поперечном сечении луча и возможность переноса энергии лучом на значительное расстояние от катода дают возможность использовать электронный луч при сварке в узкую щель, когда методы дуговой сварки не могут быть использованы;
е) рабочее расстояние «электронная пушка – изделие» можно изменять в значительных пределах без существенного изменения параметров шва. Рабочее расстояние выбирается в пределах 50–120 мм для низковольтных пушек и 50–500 мм — для высоковольтных. При этом изменение рабочего расстояния в процессе сварки на 1–5 мм не оказывает существенного влияния на качество соединения;
ж) эффективная защита металла от взаимодействия с газами в процессе сварки, осуществляемой в высоком вакууме;
з) отклонение потока электронов в магнитном поле осуществляется практически безынерционно, что дает возможность перемещать электронный луч по сложным контурам по программе с использованием электронно-вычислительной техники;
и) происходит существенное (в 8–10 раз) снижение энергетических затрат по сравнению с другими дуговыми методами;
к) ЭЛС является наиболее рациональным методом соединения изделий и конструкций:
• из тугоплавких металлов;
• из термически упрочненных металлов, когда нежелательна, затруднена или невозможна последующая термообработка;
• изделий после окончательной механической обработки при необходимости обеспечения минимальных сварочных деформаций;
• конструкций больших толщин ответственного назначения.
Недостатки метода ЭЛС:
а) сложность и высокая стоимость оборудования;
б) необходимость наличия вакуумных камер, что ограничивает размеры свариваемых изделий;
в) вредное рентгеновское излучение в процессе ЭЛС;
г) необходимость высококвалифицированного персонала.
Параметрами режима ЭЛС являются: сила тока, ускоряющее напряжение, скорость сварки, ток фокусировки. Проплавляющая способность электронного луча определяется, в основном, величиной ускоряющего напряжения и, в меньшей мере, величиной тока электронного луча. Ток в фокусирующей магнитной линзе влияет на размеры пятна нагрева и, следовательно, на величину удельной тепловой энергий. Изменяя ток фокусировки, можно изменить ширину ванны и глубину проплавления.
К числу наиболее важных технологических параметров относятся также тип и геометрия стыкового соединения и пространственное положение сварного шва и электронного пучка. Для однопроходной ЭЛС применяются типы соединений, в основном, характерные для сварки плавлением (рис. 5).
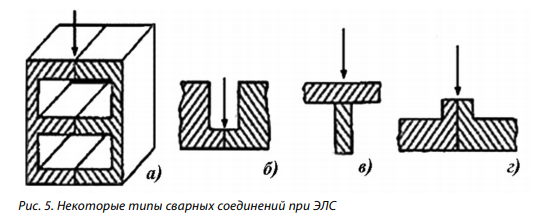
Наиболее применимыми типами соединений при ЭЛС являются:
• соединения под сварку проникающим электронным пучком (рис. 5 а);
• под сварку в углублении и труднодоступных местах (рис. 5 б);
• под сварку тавров через полку (рис. 5 в);
• отбортовка кромок (рис. 5 г), обычно применяемая в изделиях радиотехники и приборостроения.
Соединения под сварку проникающим пучком допускаются для тонколистовых металлов в нижнем положении и для металлов малых и средних толщин в горизонтальном положении.
С применением ЭЛС обычно применяются следующие технологические схемы (рис. 6):
• сварка в нижнем положении (вертикальным электронным пучком), которая выполняется как без подкладки, так и на подкладке (рис. 6 а);
• сварка на подъем и на боку (рис. 6 б и в), выполняемая горизонтальным электронным пучком без подкладки. Для предотвращения вытекания жидкого металла из сварочной ванны иногда устанавливается ограничительная планка вдоль нижней кромки стыка (рис. 6 в);
• сварка в потолочном положении (рис. 6 г), выполняемая на металлах относительно небольшой толщины (как правило, до 20 мм, применяется редко).
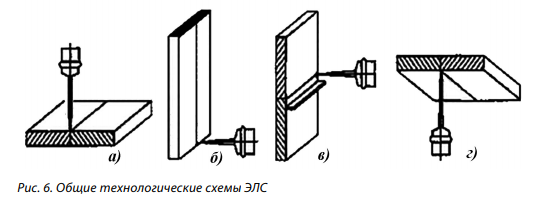
ПОДГОТОВКА ПОВЕРХНОСТИ ДЛЯ ЭЛС
Особенности подготовки стыкуемых поверхностей деталей и самих деталей обусловлены, в основном, наличием вакуума при сварке и спецификой источника теплоты в виде узкого потока электронов.
Для обеспечения высокого качества сварного шва очистке от средств консервации, загрязнений, ржавчины и оксидных пленок подвергаются в обязательном порядке стыкуемые поверхности как внешние, так и внутренние.
Предварительная очистка выполняется механически, а окончательная — в зависимости от свариваемого металла и степени шероховатости очищаемой поверхности различными физико-химическими способами.
В некоторых случаях непосредственно перед сваркой внешняя поверхность свариваемых деталей в области стыка и стыкуемые поверхности очищаются (насколько возможно через зазор в стыке) с помощью маломощного сканирующего электронного пучка. При этом пучок должен незначительно оплавлять очищаемую поверхность, не заплавляя зазор в стыке. Очистка выполняются за 1–2 прохода.
Для однопроходной ЭЛС не требуется разделки кромок. В то же время имеются определенные требования к ширине зазора в стыке: ширина зазора должна быть меньше средних поперечных размеров электронного пучка. В зависимости от типа материала, его толщины, типа стыка, пространственного положения стыка и электронного пучка, типа электронной пушки оптимальная величина зазора будет различной.
На основании многочисленных экспериментальных данных известно, что при ЭЛС без присадки металлов толщиной 20–30 мм зазор, как правило, составляет 0,1–0,2 мм, а толщиной свыше 30 мм — порядка 0,3 мм. Чем хуже свариваемость металла и выше требования к допустимой деформации, тем более высокие требования предъявляются к точности выдерживания требуемого зазора.
Разделка кромок соединяемых деталей применяется лишь в необходимых случаях для улучшения формирования шва и для обеспечения надежной работоспособности систем автоматического слежения за стыком. Например, для предотвращения или уменьшения усиления или уширения верхней части шва применяют V- или U-образные разделки кромок. В нижней части стыка иногда выполняют П- или Л-образные разделки для исключения возникновения обратного валика шва.
СПЕЦИАЛЬНЫЕ ТЕХНОЛОГИЧЕСКИЕ ПРИЕМЫ ПРИ ЭЛС
Целесообразно привести некоторые специальные технологические приемы, используемые для обеспечения ЭЛС. К ним относятся следующие приемы.
1. Полное проплавление свариваемого стыка. Это наиболее надежный и простой способ, позволяющий исключить корневые дефекты, свести к минимуму угловые деформации, уменьшить вероятность образования пор и раковин благодаря улучшению условий дегазации металла сварочной ванны.
2. Развертка электронного луча. Широко используются следующие развертки пучка: продольная, поперечная, X-образная, по окружности, эллипсу, дуге. Благодаря развертке при сварке металлов больших толщин удается резко расширить диаметр и повысить устойчивость канала в сварочной ванне, что благоприятно сказывается на стабильности формирования швов, а именно:
• уменьшается разбрызгивание расплавленного металла;
• предотвращается вытекание расплава из ванны при сварке горизонтальным пучком;
• уменьшается вероятность образования трещин, корневых дефектов и протяженных полостей.
Без применения развертки практически невозможно избежать корневых непроваров при сварке металлов больших толщин, так как весьма сложно точно направитъ узкий луч по глубокому стыку при большой протяженности шва.
3. Сварка наклонным электронным пучком. Для сварки металлов большой толщины рекомендуется постоянное отклонение электронного пучка на 5–7 град. в направлении его перемещения по изделию. Этот прием позволяет уменьшить количество пор и несплошностей.
К числу главных требований к источникам питания относятся высокая стабильность и способность подавлять развитие пробоев в пушке. Чтобы обеспечить стабильность параметров проплавления, необходимо в первую очередь добиться стабильности плотности мощности пучка на изделии при общей постоянной мощности пучка.
Колебания ускоряющего напряжения приводят к изменению диаметра пучка, а, следовательно, и плотности энергии в плоскости изделия, ввиду чего колеблется глубина проплавления. Аналогично изменяется плотность энергии в пучке на изделии вследствие колебания тока магнитной линзы при постоянном ускоряющем напряжении.
Изменение ускоряющего напряжения в пределах нескольких процентов приводит к заметному изменению глубины проплавления. Изменение тока пучка сравнительно слабо влияет на глубину проплавления, и поэтому ограничение нестабильности тока в пределах 6...10 % в большинстве случаев удовлетворяет технологическим требованиям.
Питание сварочных электронных пушек ускоряющим напряжением осуществляется от 3-фазных силовых выпрямителей. Коэффициент пульсаций в этой системе без сглаживающих фильтров составляет 6–7 % при частоте пульсаций 300 Гц. Для уменьшения пульсаций ускоряющего напряжения на выходе выпрямителя устанавливаются фильтры из конденсаторов и дросселей.
Величина допустимых пульсаций, как правило, не должна превышать 4 %. В противном случае существенно снижается глубина проплавления, наблюдаются уширение шва и разбрызгивание металла.