Введение
Как указано в [1], быстрая переналадка (Single-Minute Exchange of Dies (SMED) – быстрая смена пресс-форм) – один из многих методов бережливого производства, представляющий собой способ сокращения издержек и потерь при переналадке и переоснастке оборудования. Представляет собой набор теоретических и практических методов, которые позволяют сократить время операций наладки и переналадки оборудования. Изначально эта система была разработана для того, чтобы оптимизировать операции замены штампов и переналадки соответствующего оборудования, однако принципы быстрой переналадки можно применять ко всем типам процессов.
Создатель системы SMED Сигео Синго, в течение почти 20 лет посещая производства и наблюдая, что и как рабочие делают во время переналадки оборудования, однажды осознал, что все необходимые действия можно и нужно производить оптимальным образом. Основная идея автора системы заключается в том, что нужно отойти от шаблонного подхода к переналадке, взглянуть на этот процесс с другой стороны и найти нужное и более эффективное решение.
Система SMED является довольно простым и универсальным решением, которое успешно используется по всему миру. Логика SMED основана на двух ключевых принципах:
1. Разделение операций по переналадке на внутренние и внешние действия.
2. Преобразование как можно большего числа внутренних действий переналадки во внешние позволяет в несколько раз сократить время переналадки.
Внутренние действия по переналадке – это операции, которые выполняются только после остановки и/или выключения оборудования. Например, пресс-форму или систему фильтрации можно заменить только при остановке единицы оборудования.
Внешние действия по переналадке – это операции, которые можно выполнять во время работы оборудования. Например, болты крепления прессформы для следующего изделия можно отобрать и отсортировать еще при работающем станке, так же как и собрать и проверить систему фильтрации для следующего продукта. Преобразование как можно большего числа внутренних операций переналадки во внешние позволяет в несколько раз сократить время переналадки оборудования.
Преобразование как можно большего числа внутренних операций переналадки во внешние позволяет в несколько раз сократить время переналадки оборудования.
Сигео Синго признавал восемь методов [4], которые следует учитывать при осуществлении SMED:
− Отделение внутренних операций установки от внешних.
− Преобразование внутренних операций установки во внешние.
− Стандартизация функций, а не форм.
− Использование функциональных зажимов или ликвидация крепежа вообще.
− Использование промежуточных приспособлений.
− Использование параллельных операций.
− Устранение корректировок.
− Механизация.
Обоснование необходимости метода SMED
Как указывается в [2], производственный процесс – это некая последовательность действий по превращению сырья в готовые изделия. Проще говоря, процесс – это то, как что-то делается. Производственные процессы разделяются на пять основных стадий:
− подготовка;
− обработка;
− контроль;
− транспортировка;
− хранение.
Подготовка включает в себя очистку, демонтаж и сборку.
Обработка обеспечивает изменение формы или свойств материалов.
Контроль подразумевает сравнение со стандартом.
Транспортировка – это перемещение продукции.
Соответственно, хранение – это период, в течение которого обработка, транспортировка или контроль продукции не происходят. Каждая стадия производственного процесса состоит из операций по переналадке, т. е. операций по подготовке или регулировке оборудования, которые выполняются до и после обработки каждой партии изделия.
Многие компании производят свою продукцию большими партиями только потому, что длительность процесса переналадки делает процесс замены продукции на линии очень дорогостоящим.
Потери, связанные с простоем оборудования, иногда исчисляются миллионами рублей. В то же время изготовление продукции крупными партиями также имеет несколько недостатков:
− задержки;
− потери, связанные с запасами продукции;
− ухудшение качества.
Многие компании производят свою продукцию большими партиями только потому, что длительность процесса переналадки делает процесс замены продукции на линии очень дорогостоящим. Потери, связанные с простоем оборудования, иногда исчисляются миллионами рублей.
Заказчикам приходится дожидаться, пока предприятие изготовит всю партию продукта (изделия), хотя достаточно было бы произвести и меньшее количество. Последующее хранение нереализованной продукции порождает дополнительные затраты, требует привлечения других ресурсов предпри ятия и увеличивает вероятность того, что эту продукцию придется направить в переработку или даже на уничтожение в связи с порчей.
Естественно, все это не добавляет ценности продукту (изделию).
Традиционная переналадка
Независимо от типа используемого оборудования все процедуры традиционной переналадки (то есть без использования системы SMED) состоят из четырех этапов:
1. Подготовка, регулировка, проверка материалов и инструментов.
2. Монтаж и демонтаж съемных элементов.
3. Измерения, настройка и калибровка.
4. Пробные пуски и калибровка.
На первом этапе (при подготовке, регулировке и проверке инструментов) проверяется наличие, правильное местоположение и работоспособность всех деталей, съемных частей и инструментов. В системе традиционной переналадки все подготовительные действия выполняются уже после остановки оборудования.
На втором этапе традиционной переналадки с оборудования снимаются съемные элементы, детали, производится их очистка и т. п. На данном этапе также может производиться установка новых инструментов для обработки следующей партии изделий. Эти действия выполняются после того, как завершена обработка партии изделий. Как правило, такие действия выполняются при отключенном оборудовании и относятся к операциям внутренней наладки. Из табл. 1 видно, что этот этап, то есть непосредственно переналадка, занимает по сравнению с другими этапами гораздо меньше времени.
Третий этап (измерения, настройка и калибровка) включает все работы по измерению и калибровке для обеспечения производства, например центровка, задание размеров, температуры, давления и т. п. В большинстве случаев для проведения таких работ также требуется остановка оборудования.
И последний, четвертый этап (пробные пуски и регулировка) подразумевает работы по корректировке, выполнению пуска оборудования и производство пробной единицы изделий. Получается, что чем точнее и аккуратнее были произведены измерения и регулировка на предыдущем этапе, тем проще провести регулировку оборудования на этом этапе. Соответственно, при традиционной переналадке время, затрачиваемое на пробные пуски и регулировку оборудования, зависит от квалификации и опыта рабочего. Как показано в табл. 1, на этот этап тратится около 50% всего времени переналадки. При традиционной переналадке оборудование производит некачественную продукцию до тех пор, пока не завершится данный этап. Поэтому регулировка и пробные пуски относятся к операциям внутренней наладки.
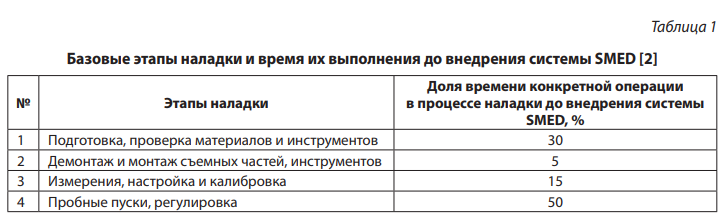
Источник: Quick Changeover for Operators. The SMED System by Shigeo Shingo, 2000
Основная причина, из-за которой традиционные операции переналадки занимают много времени, заключается в том, что операции внутренней и внешней наладки перемешаны между собой.
Основная причина, из-за которой традиционные операции переналадки занимают много времени, заключается в том, что операции внутренней и внешней наладки перемешаны между собой.
Многие задачи, выполнить которые можно и при работающем оборудовании, выполняются только после его остановки.
Как было указано выше, заготовительное или механосборочное производств опроизводит продукцию крупными партиями просто потому, что длительное время переналадки не позволяют без потерь часто менять производимые изделия.
− Большие партии – потери от запасов. Хранение того, что не собрано в сборочном производстве и не продано, стоит денег и замораживает финансовые и материальные ресурсы.
− Большие партии – задержки. Заказчику приходится ждать, пока цех произведет всю партию, а не то количество и комплект деталей, которые ему необходимы.
− Снижение качества. Изменились требования к конструкции – большой задел идет в брак или требуется доработка. Хранение непроданных запасов увеличивает шансы повреждения и необходимости доработки перед продажей, что увеличивает себестоимость продукции.
Система SMED (Single Minute Exchange of Dies – быстрая замена штампов) позволяет отказаться от предубеждения, что переналадка требует значительного времени. Если процесс переналадки занимает очень мало времени, ее можно проводить так часто, как это требуется.
Это, в свою очередь, означает, что если мы будем производить продукцию малыми партиями, то сможем получить много преимуществ. При этом в [2] говорится о следующих преимуществах, которые дает внедрение SMED:
− Гибкость: фирмы могут реагировать на изменяющиеся требования заказчиков, не производя излишних запасов.
− Сокращение сроков поставки: производство малыми партиями сокращает сроки поставки деталей и комплектов деталей.
− Улучшается качество: сокращение запасов дает сокращение дефектов и повреждений при хранении и транспортировке. SMED сокращает также потери за счет уменьшения возможности ошибок при переналадке и исключения пробных партий при переходе на новое изделие.
− Повышение производительности: сокращение времени переналадки позволяет снизить простои оборудования, что означает увеличение отдачи от него.
− Сокращение НЗП – на столько же, на сколько удалось ускорить переналадку, экономия средств, замороженных в НЗП.
− Не требуются высококвалифицированные наладчики, так как процесс наладки становится проще, ее может выполнять оператор или другой рабочий без большого опыта и квалификации.
Как указано в [6], суть метода заключается в сокращении общего эффективного времени, затраченного в результате перехода с одной продукции на другую (времени переналадки). Снижение времени переналадки часто считают целью метода, но это совершенно неправильно, не стоит путать цели и сред ства. Сей инструмент был разработан в компании «Тойота» для сокращения размеров партий изготавливаемых продуктов, так как высокое время переналадки требовало работу большими партиями, что приводило к скоплению запасов, повышению расходов на их обработку и эксплуатацию складов, не говоря уже о замороженном в этих запасах капитале.
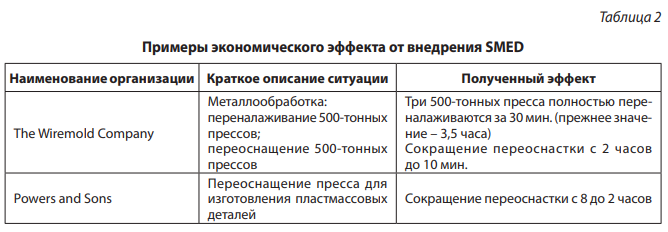
Другими словами, инструмент позволял избавиться от нескольких видов потерь. Предприятие может удовлетворить меняющиеся потребности заказчиков без издержек на хранение запасов продукции. Производство малыми партиями позволит сократить время, затрачиваемое на подготовку заказа к отправке, а также время ожидания заказчиком требуемой продукции. Соответственно, снижается вероятность порчи изделий, поскольку сокращается время их хранения. Уменьшается и объем производственного брака из-за меньшего числа ошибок в ходе наладки и пробных пусков оборудования.
В табл. 2 приводятся примеры экономии, полученной различными предприятиями и организациями в мире, которые внедрили у себя SMED (цит. по [5]).
Система SMED (Single Minute Exchange of Dies – быстрая замена штампов) позволяет отказаться от предубеждения, что переналадка требует значительного времени.
Возможности системы SMED
В то же время система SMED призвана упростить и сократить действия при переналадке. Например, она позволяет сократить время операций на третьем этапе традиционной переналадки, предлагая производить все или большинство подготовительных операций при работающем оборудовании, а также обеспечить изготовление качественной продукции сразу же после запуска без пробных запусков и регулировки, другими словами, полностью отказаться от четвертого этапа традиционной переналадки.
Система SMED внедряется в четыре этапа: один подготовительный и три основных (рис. 1). Подготовительный этап, так называемый анализ процесса наладки, помогает разобраться в том, как именно выполняются процессы наладки каждой конкретной единицы оборудования.
Этап 1 – разграничение операций внешней и внутренней наладки. Только благодаря первому этапу можно сократить простои оборудования, происходящие в процессе переналадки, на 30–50%.
Этап 2 – трансформация некоторых операций внутренней наладки в катего рию внешних. Второй этап позволяет еще больше сократить время переналадки.
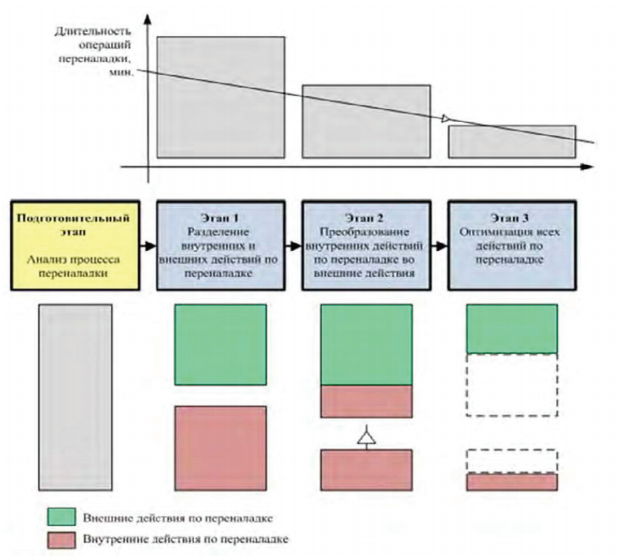
Рис. 1. Этапы внедрения системы SMED [2]
Как указано в [3], быстрая переналадка, или SMED (Single-Minute Exchange of Dies – дословно «быстрая смена прессформ»), – это методика, представляющая собой набор организационных и технических методов, которые используются для сокращения времени переналадки или переоснастки оборудования.
Общая структура проведения программы SMED
1. Выбор объекта улучшения.
2. Создание рабочей группы.
3. Описание процесса переналадки (хронометраж).
4. Этап 1: разбиение этапов на внутренние и внешние.
5. Этап 2: перевод всех возможных этапов переналадки во внешние.
6. Этап 3: оптимизация времени выполнения всех этапов переналадки (технические и организационные методы).
7. Повторный хронометраж по итогам программы и установка целевого показателя.
8. Разработка мероприятий по дальнейшему совершенствованию.
9. Установка стенда отслеживания целевых показателей SMED.
10. Подготовка итоговой презентации.
Производство малыми партиями позволит сократить время, затрачиваемое на подготовку заказа к отправке, а также время ожидания заказчиком требуемой продукции.
Опишем стадии процесса более подробно.
Выбор объекта улучшения
Для выбора объекта для проведения SMED необходимо провести анализ оборудования на предприятии для выявления критичных единиц (узких мест). Впоследствии полученный опыт можно распространить на аналогичное оборудование.
Создание рабочей группы
Наиболее эффективно задачу снижения времени переналадки оборудования решают рабочие группы в составе:
− специалист от производства – руководитель группы;
− операторы, работающие на оборудовании;
− специалист по бережливому производству – методический руководитель группы;
− специалист службы главного технолога (при наличии таковой);
− специалист службы главного механика и т. д.
* Руководитель группы ставит перед остальными участниками проекта конкретные, измеримые цели.
Описание процесса переналадки
Группа выходит на производственную площадку (Gemba) и первоначально описывает текущее состояние, разбивая процесс на составляющие его элементы и переходы. Далее проводится хронометраж (видеосъемка) и параллельно – выявление проблем, влияющих на безопасность и время выполнения элементов.
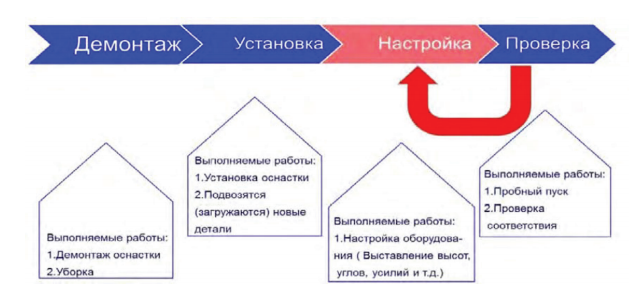
Рис. 2. Разделение внутренней и внешней переналадки, преобразование внутренней переналадки во внешнюю [3]
Основные работы при переналадке [3]
Группа определяет, какие элементы относятся к внутренней переналадке, а какие выполняются без остановки оборудования. Составляется список необходимого для осуществления переналадки технологического оснащения. Проводится анализ собираемых данных (по переналадкам на разные виды изделий) и определяется возможность выполнения элементов внутренней переналадки без остановки оборудования (преобразование внутренней переналадки во внешнюю).
Оптимизация времени выполнения всех этапов переналадки
Для достижения наилучшего результата на всех этапах внедрения системы SMED рекомендуется проводить мозговой штурм: группа в полном составе собирается после каждой переналадки.
Поочередно зачитываются проблемы, обнаруженные каждым членом группы.
Вырабатываемые варианты решений каждой проблемы записываются в бланк плана мероприятий.
Организационные методы
Методы, основанные на стандартизации и регламентации действий по переналадке:
* Перевести как можно больше внутренних операций во внешние.
Технические методы
Методы, основанные на доработке существующей и установке новой технологической оснастки:
* Стандартизировать функции, а не форму. Стандартизация формы и размеров штампов может значительно снизить время наладки. Однако стандартизация формы требует значительных затрат. С другой стороны, стандартизация функции требует только однородности деталей, необходимых для операций наладки.
* Использовать стандартизированные зажимы или вообще отказаться от крепежа.
* Использовать зажимные и переходные приспособления.
* Ликвидировать корректировки.
Обычно корректировки и пробный запуск занимают 50–70% времени внутренней наладки. Их устранение дает поразительную экономию времени.
Механизировать и автоматизировать труд
Часто используемую оснастку расположить в непосредственной близости от оборудования.
Визуализировать оснастку и рабочие параметры оборудования
* По возможности проводить часть операций параллельно.
Некоторые из задержек, связанные с регулировками при внутренней наладке, можно устранить путем использования стандартных приспособлений. Когда обрабатывается заготовка, закрепленная в одно приспособление, следующая заготовка устанавливается во второе приспособление. Когда обработка первой заготовки закончена, второе приспособление легко ставится на станок для обработки.
* Использование Poka-Yoke (пока-екэ).
Повторный хронометраж по итогам программы и установка целевого показателя
Проводится повторный хронометраж (видеосъемка) для оценки эффективности мероприятий и установки целевых показателей.
Быстрая переналадка, или SMED (Single-Minute Exchange of Dies – дословно «быстрая смена пресс-форм»), – это методика, представляющая собой набор организационных и технических методов, которые используются для сокращения времени переналадки или переоснастки оборудования.
Разработка мероприятий по дальнейшему совершенствованию
Оформление стенда
После завершения программы SMED для закрепления результата оформляется стенд для отслеживания времени переналадки.
Индикаторы стенда:
* Контрольный лист с перечнем всех необходимых инструментов и оснастки для выполнения операции переналадки.
Несколько иная схема реализации SMED приводится в [7]. Данная схема реализации описана применительно к машиностроительному предприятию.
При этом стандартный алгоритм для запуска быстрой переналадки (SMED) – 14 шагов:
1. Определить проблемные этапы процесса переналадки и оценить, какой эффект применение SMED принесет всей системе.
2. Выбрать определенные станки или рабочую зону для проведения мероприятий по сокращению времени настройки или переналадки.
3. Сформировать команду по сокращению времени переналадки.
4. Организовать обучение и тренинги по внедрению SMED.
5. Изучить и документально зафиксировать ход и длительность текущего процесса настройки или переналадки (через графики, видео). При оптимизации процесса отталкивайтесь от этих данных.
6. Разделить операции по переналадке на три группы:
− потери – операции, которые не создают ценности;
− обязательные внутренние операции – операции, которые могут проводиться только при выключенном оборудовании;
− обязательные внешние действия;
− операции, которые могут проводиться без выключения оборудования.
7. Устранить потери – избавьтесь от лишних операций.
8. Трансформировать как можно больше внутренних операций по переналадке во внешние.
9. Провести оптимизацию внутренних операций по переналадке:
− использовать специальную передвижную подставку для инструментов;
− использовать более легкие в обращении карабины вместо зажимов и гаек;
− использовать стопорные механизмы, чтобы быстро менять положение зажимов;
− использовать подвижные балки вместо подъемных кранов;
− использовать подвесные механизмы для работы с тяжелыми зажимами;
− по возможности использовать формы стандартного размера;
− стандартизировать размер и тип болтов, отверток и т. д.
10. Провести оптимизацию внешних операций по переналадке:
− внедрить принципы визуального контроля;
− использовать чек-листы, чтобы ускорить проверку готовности оборудования и снизить риск ошибки;
− использовать специальную подставку для организации инструментов;
− провести организацию рабочей зоны (5S), чтобы сократить время на поиск нужных инструментов.
11. Разработать стандартные операционные процедуры (SOP).
12. При необходимости провести обучение и организовать тренинги по SMED для закрепления полученного опыта.
Ликвидировать корректировки. Обычно корректировки и пробный запуск занимают 50–70% времени внутренней наладки. Их устранение дает поразительную экономию времени.
13. Изучить и оценить эффективность нового процесса настройки или переналадки.
14. Вернитесь к пункту 5 и подготовьтесь к новому поиску возможностей сокращения времени переналадки.
В ряде случаев рекомендуется перед тем, как начать работу по внедрению SMED, провести работы по разработке и внедрению 5S. И после реализации метода SMED также завершить методом 5S.
В ряде случаев рекомендуется перед тем, как начать работу по внедрению SMED, провести работы по разработке и внедрению 5S. И после реализации метода SMED также завершить методом 5S.
То есть реализовать следующую последовательность действий:
1. Начинаем с внедрения системы 5S.
2. Переводим внутренние операции во внешние.
3. Гарантировать, что работник не отходит от оборудования все время наладки.
4. Использовать быстрые соединения (никаких болтов!).
5. Организовать корректное позиционирование и стандарты (никаких доводок!).
6. Использовать метод работы «вставляй и включай (никаких настроек!)».
7. Стандартизировать операции переналадки.
8. Завершаем также с 5S.
Заключение
Система SMED демонстрирует новый взгляд на процесс переналадки. Оперативная переналадка сокращает время простоя оборудования. Сокращение времени простоя оборудования делает работу более равномерной и спокойной. Более простой процесс наладки гарантирует бoльшую безопасность производства – меньше физических нагрузок или риска получения травм рабочими. Меньше запасов означает меньше суматохи на рабочем месте, что делает производственный процесс легче и безопаснее. Инструменты для наладки стандартизированы, поэтому следить нужно за меньшим числом инструментов. В результате внедрения SMED мы можем получить значительное увеличение производительности и снижение себестоимости изготавливаемой продукции.