Сегодня для многих российских предприятий из-за высокой инфляции существенной проблемой является повышение себестоимости производства, многие уже сейчас работают с отрицательной рентабельностью. Таким предприятиям жизненно важно найти рычаги для снижения себестоимости продукции. Это первая причина ознакомиться с системой менеджмента бережливого производства.
Известно, что качество любого продукта или товара напрямую зависит от результативности функционирования процессов, а один из важнейших показателей совершенства процесса — от сутствие потерь. Это вторая из причин ознакомиться с системами менеджмента бережливого производства.
ISO 22000, СМБП, ХАССП
Одной из основных систем менеджмента, которыми пользуются производители молочной продукции, является система менеджмента безопасности пищевой продукции на основе стандарта ISO 22000. Этот стандарт внедрен более чем в 150 странах на более чем 30 тыс. предприятий [2]. В июне 2018 года было принято его второе издание.
В России широко применяются стандарты, основанные на принципах ХАССП: ГОСТ Р ИСО 22000-2007 «Системы менеджмента безопасности пищевой продукции. Требования к организациям, участвующим в цепи создания пищевой продукции», а также ГОСТ Р 51705.1 «Управление качеством пищевых продуктов на основе принципов ХАССП».
С 15 февраля 2015 года, согласно п. 2 ст. 10 ТР ТС 021/2011 «О безопасности пищевой продукции», внедрение процедур, основанных на принципах ХАССП, обязательно для всех компаний, занимающихся изготовлением пищевой продукции на территории РФ и других стран Таможенного союза.
Если выполнение требований ISO 22000, внедрение процедур, основанных на принципах ХАССП, обеспечивает выпуск безопасной продукции, то какую ценность организации принесет внедрение системы менеджмента бережливого производства?
В основе бережливого производства заключена концепция организации бизнеса, ориентированная на создание привлекательной ценности для потребителя путем формирования непрерывного потока создания ценности с охватом всех процессов организации и их постоянного совершенствования через вовлечение персонала и устранение всех видов потерь.
С 2014-го по 2019 год в России разработаны и введены в действие 14 государственных стандартов, содержание которых понятно из их названий:
• ГОСТ Р 56404-2015 «Бережливое производство. Требования к системам менеджмента»;
• ГОСТ Р 56405-2015 «Бережливое производство. Процесс сертификации систем менеджмента. Процедура оценки»;
• ГОСТ Р 56406-2015 «Бережливое производство. Аудит. Вопросы для оценки системы менеджмента»;
• ГОСТ Р 56407-2015 «Бережливое производство. Основные методы и инструменты»;
• ГОСТ Р 56906-2016 «Бережливое производство. Организация рабочего пространства (5S)»;
• ГОСТ Р 56907-2016 «Бережливое производство. Визуализация»;
• ГОСТ Р 56908-2016 «Бережливое производство. Стандартизация работы»;
• ГОСТ Р 57523-2017 «Бережливое производство. Руководство по системе подготовки персонала»;
• ГОСТ Р 57524-2017 «Бережливое производство. Поток создания ценности»;
• ГОСТ Р 57522-2017 «Бережливое производство. Руководство по интегрированной системе менеджмента качества и бережливого производства»;
• ГОСТ Р 58524 – 2019 БП. Особые требования по применению бережливого производства в организациях и цепях поставок автомобильной промышленности;
• ГОСТ Р 58589 – 2019 БП. Особые требования по применению бережливого производства в судостроительной промышленности;
• ГОСТ Р 58581 – 2019 Бережливое производство «Особые требования по применению бережливого производства в авиационной промышленности и организациях, производящих соответствующие запасные части».
...Качество любого продукта или товара напрямую зависит от результативности функционирования процессов, а один из важнейших показателей совершенства процесса — отсутствие потерь...
Очень рекомендуем хотя бы бегло их посмотреть. Это не переведенные с другого языка стандарты, а отечественные разработки. В мировой практике аналогов нет. Они создавались большим кругом блестящих отечественных ученых, практиков-консультантов, руководителей высокотехнологичных и наукоемких компаний и предприятий. В списке разработчиков — ПАО «КАМАЗ», «Группа ГАЗ», ПАО «Татнефть», госкорпорация «Росатом», ОАО «РЖД» и др. Стандартами по бережливому производству вводятся важные концептуальные понятия, знание которых необходимо руководителям, желающим улучшить результаты деятельности своих предприятий. Рассмотрение производственных процессов через призму бережливого производства (далее — БП) выявляет трудноуловимые при обычном анализе нестыковки и потери.
...В основе бережливого производства заключена концепция организации бизнеса, ориентированная на создание привлекательной ценности для потребителя путем формирования непрерывного потока создания ценности с охватом всех процессов организации и их постоянного совершенствования через вовлечение персонала и устранение всех видов потерь...
На схеме отражена взаимосвязь между стандартами по качеству, производственными системами и стандартом по системе менеджмента бережливого производства (СМБП).
Причины появления концепции бережливого производства за рубежом
Основы системы бережливого производства были заложены Генри Фордом, хотя в начале 1920-х годов в Америке слово «бережливое» (lean) в отношении производственных процессов еще не применялось. Генри Форд первым сумел полностью раскрыть потенциал массового производства путем правильной установки сборочных линий и взаимозаменяемости деталей, существенно сократив издержки и повысив качество автомобилей. Принципы массового производства от Ford перенял другой американский гигант автомобилестроения — General Motors, а вскоре они получили широкое распространение и на предприятиях Европы. При всех своих плюсах фордовские идеи организации производства имели ряд существенных недостатков, главными среди которых можно считать выпуск продукции крупными партиями, трудность перехода на производство новых марок автомобилей, крайнюю централизацию управления, большие запасы материалов и полуфабрикатов на складах.
Новый метод управления производством пришел из послевоенной Японии как результат работы Kaizen Group, изучавших американские методы обучения в промышленности (концепция TWI), идеи У. Деминга, Д. Джурана и А. Фейгенбаума — создателей системы всеобщего управления качеством (Total Quality Management, TQM). Японцы начали реформы производственных процессов в автомобилестроении, поскольку требовалось снизить себестоимость машин (японские были в 10 раз дороже американских), синхронизировать все действия в цехах и так наладить работу с поставщиками, чтобы все материалы поступали своевременно и в нужном количестве.
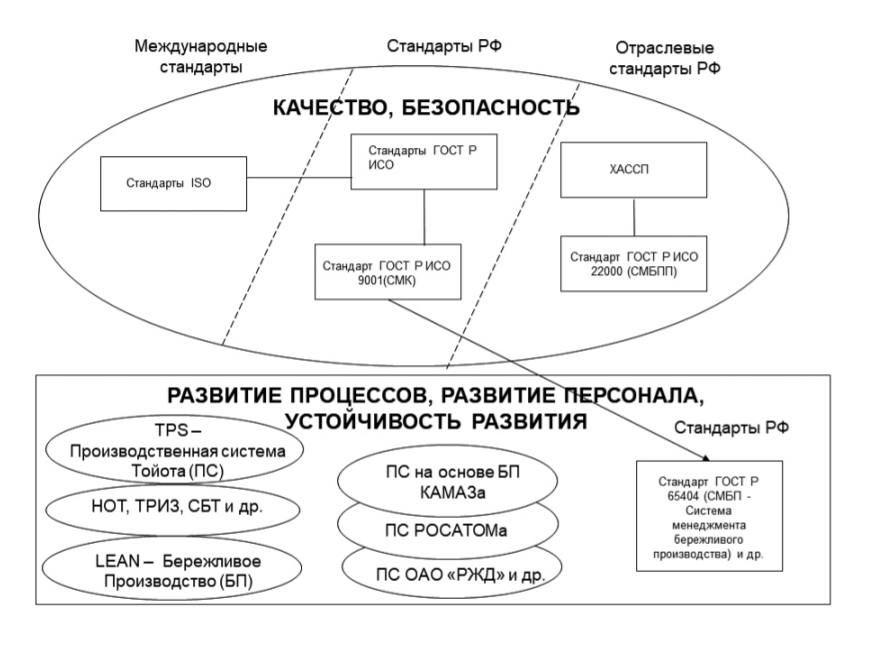
В 1950-х годах Тайити Оно для компании «Тойота» разработал систему Toyota Production System (TPS), основанную на принципе вытягивания именно той продукции, которая нужна в данный момент на рынке. Принцип вытягивания применялся и в производственных цехах при помощи картонных карточек с информацией (канбан). Коллега Тайити Оно — Сигео Синго внес существенный вклад в развитие теории и практики производства нового типа, разработав метод быстрой переналадки (SMED), предназначенный для устранения потерь при переходе на выпуск нового вида продукции. Другой японский специалист в области бережливого производства — Масааки Имаи, первым стал распространять философию кайдзен, идеи которой вытекают также из концепции бережливого производства.
За 30 лет, пока TPS формировалась в устойчивую и определенную систему, когда стали очевидны ее плоды, а принципы и инструменты были формализованы и описаны, Япония превратилась в великую экономическую державу, ее высокотехнологичные и высококачественные товары хлынули на американский и мировой рынок. Япония успешно продавала и до сих пор успешно продает не только автомобили, мотоциклы и электронику, но и продукцию не самой сложной конструкции, например железнодорожные рельсы.
По причине чрезвычайно успешного выхода «Тойоты» на американский рынок теперь уже крупнейшие автомобилестроительные компании в США стали пристально изучать японский опыт новой организации производства. С 1985 года группа американских исследователей в Массачусетском технологическом институте в течение пяти лет изучала опыт предприятий как в Японии, так и в других развитых странах (международная программа «Автомобили»). При составлении отчета о проделанной работе один из исследователей, Джон Кравчик, впервые использовал термин Lean Production для отражения того факта, что речь идет о чем-то гораздо большем, чем конкретная система производства в «Тойоте». В понимании Джона Кравчика, а теперь и всего мира, бережливое производство ассоциируется с производственной системой, в которой нет ничего лишнего. Поэтому на русский язык Lean Produсtion переводится часто как «малозатратное, рачительное, гибкое производство».
В ГОСТ Р 56020-2014 дано определение бережливого производства как «концепции организации бизнеса, ориентированной на создание привлекательной ценности для потребителя путем формирования непрерывного потока создания ценности с охватом всех процессов организации и их постоянного совершенствования через вовлечение персонала и устранение всех видов потерь».
...В понимании Джона Кравчика, а теперь и всего мира, бережливое производство ассоциируется с производственной системой, в которой нет ничего лишнего. Поэтому на русский язык Lean Produсtion переводится часто как «малозатратное, рачительное, гибкое производство»...
В мировом масштабе принципы, методы и инструменты БП с 1990-х годов стали активно внедрять на своих производствах автомобилестроители, компании авиационной, электронной промышленности, транспортного машиностроения, железнодорожные компании в США, Канаде, Китае, Европе. Следом за ними в сторону бережливости двинулись не связанные со сборкой механизмов представители легкой промышленности, медицинские и государственные учреждения.
Научный подход к организации труда в СССР
В СССР, когда экономика была плановой и централизованной, повышение производительности труда было поставлено на научные основы. В 1921 году был организован Центральный институт труда при ВЦСПС, которым долгое время руководил Алексей Капитонович Гастев (1882–1939). Он много энергии и сил уделял вопросам стандартизации, состоял в переписке с Генри Фордом и хорошо знал его инновационные идеи, как и идеи основателя конвейерного производства Ф. Тейлора. В честь А.К. Гастева с 2011 года в России ежегодно проводится конкурс на Кубок лидеров производительности.
В послевоенные годы и до распада Советского Союза существовало множество отечественных методов совершенствования труда и концепций работы с проблемами: метод Ковалева, система А.С. Родова, БИП, ТРИЗ, КАНАРСПИ, СБТ, НОРМ, КС УКП, КС ПЭП и КР и др. Формат статьи не позволяет дать их развернутый анализ и оценку, но все они работали, обеспечивая качество продукции и эффективность производственных процессов. Не случайно приходится иногда слышать во время тренингов горестные сетования людей старшего поколения: «Что вы нам тут рассказываете про всякую муду (яп. “потери”), 5S и покиёки (яп. “защита от ошибок”), у нас все это было».
Производственные системы в современной России
Одной из заметных тенденций в послеперестроечный период стало создание отечественных производственных систем (ПС) на основе идеологии бережливого производства. Они создаются на авиационных, металлургических предприятиях, в органах госслужбы, медицинских и образовательных учреждениях. С каждым годом растет число участников конкурса на Кубок лидеров производительности им. А.К. Гастева, оценивающего степень развития производственных процессов, развития сотрудников и саму степень устойчивости развития.
В ГОСТ Р 56406-2015 «Бережливое производство. Аудит. Вопросы для оценки системы менеджмента» есть чек-лист. Ответив на 129 вопросов и подсчитав баллы, можно самим определить, на каком из семи уровней зрелости находится система менеджмента бережливого производства на вашем предприятии. Начальный уровень, от 0 до 52 баллов, называется «намерение соответствовать требованиям СМБП», высший уровень, от 206 до 258 баллов, — «деловое совершенство».
В 2012 году известный в России специалист по технологиям бережливого производства Валерий Казарин написал после своего выступления на VII Международном технологическом форуме «Инновационные технологии и оборудование в молочной промышленности»: «Практически 95% присутствующих в аудитории сказали, что не знают, что такое бережливое производство» [6]. Поиск в отраслевой печати и Интернете дал лишь несколько примеров внедрения принципов и инструментов БП молочными компаниями и предприятиями. Однако в обнаруженных источниках ничего не говорится о применении стандартов по бережливому производству.
В 2015 году в электронном журнале «Промышленная и экологическая безопасность, охрана труда» была опубликована небольшая статья о внедрении БП на ОАО «МК “Сарапул-молоко”», ОАО «МИЛКОМ», входящем в агропромышленный холдинг «КОМОС ГРУПП» [7].
В статье, опубликованной в журнале «Молочная промышленность» [4], упомянуто, что на Архангельском молочном заводе — АО «Молоко» в 2017 году стартовал проект «Бережливое производство». АО «Молоко» принимало участие в конкурсе на Кубок А.К. Гастева. Мы связались с заместителем генерального директора по коммерческим вопросам и маркетингу агрохолдинга «Белозорие» Любовью Сыровенко и узнали, как в АО «Молоко» идет процесс внедрения БП (об этом будет подробнее в конце статьи). Также среди российских лин-предприятий значится агрохолдинг «Кубань», в состав которого входят современные молочные фермы [8]. Какие именно инструменты БП внедрены в агрохолдинге «Кубань», на сайте www.leaninfo.ru не уточняется.
Исходя из столь скудных сведений можно констатировать, что система менеджмента бережливого производства в настоящее время не находит должного внимания со стороны предприятий молочной промышленности. Национальные стандарты (ГОСТы) по бережливому производству, перечень которых был приведен выше, остаются без применения. А «Рекомендации по применению принципов бережливого производства в различных областях промышленности», утвержденные приказом Минпромторга России в 2017 году, вероятно, восприняты деловым сообществом в молочной промышленности как сугубо рекомендательный документ.
Почему же производители и переработчики молока так отстают от других отраслей, в которых идет кропотливая работа над совершенствованием своих производственных систем? В министерствах здравоохранения, образования, в государственных органах составляются многолетние программы, разрабатываются методики, рекомендации и пособия по внедрению инструментов БП. Для обсуждения вопросов создаются ассоциации и форумы. Можно ли решить все вопросы по снижению себестоимости и улучшению процессов только путем инвестиций в техническую модернизацию и соблюдения требований стандартов по качеству молочных продуктов?
Философия бережливого производства основана на представлении бизнеса как потока создания ценности для потребителя, гибкости, выявлении и сокращении потерь, постоянном улучшении всех видов деятельности на всех уровнях организации, вовлечении и развитии персонала с целью повышения удовлетворения потребителей и других заинтересованных сторон. В БП используется следующий понятийный аппарат.
...Философия бережливого производства основана на представлении бизнеса как потока создания ценности для потребителя, гибкости, выявлении и сокращении потерь, постоянном улучшении всех видов деятельности на всех уровнях организации, вовлечении и развитии персонала с целью повышения удовлетворения потребителей и других заинтересованных сторон...
Поток создания ценности
Все материальные процессы на предприятии являются потоками создания ценности (ПСЦ). В соответствии с ГОСТ Р 56020-2014 «поток создания ценности — деятельность, направленная на создание ценности для потребителя, которая реализуется при помощи системы взаимосвязанных процессов/операций. Результаты деятельности процессов/ операций, как материальные, так и не материальные, передаваемые от одного процесса/операции к другому, создают поток ценности. Данные потоки характеризуются скоростью, непрерывностью, равномерностью, а также сопровождаются различными видами потерь. В БП стремятся увеличить скорость потока ценности, обеспечить его непрерывность, равномерность и устранить потери. В качестве основных характеристик ценности рассматриваются характеристики качества, безопасности, а также стоимостные характеристики продукции/услуги».
Достаточно сложную формулировку можно свести к трем основным задачам, которые решаются с помощью БП:
— увеличение скорости производственных процессов;
— обеспечение их непрерывности и равномерности;
— устранение в них потерь.
Даже если кажется, что какой-нибудь процесс идеально настроен и протекает максимально быстро, надо помнить, что основные потери происходят на стыках/объединении/разъединении/параллелизации процессов или когда процесс преобразует выходы в одном подразделении во входы в другом. Как правило, в организациях, начинающих внедрять БП, составляются карты потоков создания ценности (КПСЦ), протекающие по горизонтали на самом низовом уровне, то есть на уровне операций. Или на уровне отдела и цеха, когда картируется процесс, подконтрольный одному начальнику. Такой подход объясним тем, что все наши предприятия основаны на вертикальной иерархии, фрагментируя ответственность за показатели большинства горизонтальных процессов. В нормальных условиях процесс может не давать сбоев и большого разброса показателей эффективности и качества, но при необходимости его ускорить или перенастроить на другой ассортимент продукции процесс может развалиться на части и привести к выпуску брака.
Время производственного цикла (production lead time)
Согласно ГОСТ Р 56020-2014, это «время прохождения продукции через весь процесс или поток создания ценности от первой операции до последней». Тут важно концептуально понимать, что мерилом успешности применения инструментов БП является сокращение времени цикла изготовления качественной продукции, то есть SKU1, или оказания услуги.
Время такта (takt time)
Доступное производственное время за определенный период (смену, сутки, месяц и т.д.), деленное на объем потребительского спроса за этот период. Цикл должен соответствовать такту производства, чтобы ритмично передавать заказчику ожидаемый им продукт. Если производственный цикл короче такта, появляется излишек времени, начинает простаивать оборудование, а люди — слоняться без дела. Когда цикл длиннее, вскипает «авральная нервотрепка», нарушаются требования технологий и правил безопасности труда.
Карта потока создания ценности (value stream mapping, VSM)
КПСЦ — схема, изображающая каждый из этапов материального и информационного потока, необходимых для выполнения заказа потребителя. Наличие таких карт, а чем их больше, тем лучше, является очевидным свидетельством работы руководства над улучшением процесса (проектированием его будущего состояния). Из карты видна длительность цикла, а все действия процесса (потока) распределены на три группы:
— добавляющие ценность для потребителя;
— не добавляющие ценности, но необходимые для поддержания процесса и которые могут быть сокращены;
— действия, которые ценности не добавляют и процесс никак не поддерживают. Такие действия выделяются в отдельную группу — «Потери», и специалисты начинают думать, каким методом или инструментом БП их можно устранить.
Потери
В ГОСТ Р 56020-2014 указаны семь основных видов потерь (яп. «муда»):
1) перепроизводство — продукт/ услуга производится в большем объеме, чем требуется заказчику
2) избыток запасов — хранение любых запасов в количестве, существенно превышающем минимально необходимое;
3) транспортировка — лишнее движение материалов;
4) ожидание — большие простои между этапами производства продукта / выполнения услуги;
5) чрезмерная обработка — лишняя обработка / действия из-за несоответствующих инструментов или плохой конструкции продукта (как результат несоответствующего планирования и проектирования услуги);
6) перемещения — лишние движения человека, потери при подборе материалов, поиске компонентов, инструментов, информации, документов;
7) выпуск дефектной продукции — доработка и отбраковка несоответствующей продукции / ненадлежащего выполнения услуги.
Существует еще один вид потерь — потеря творческого потенциала у сотрудников. Его трудно измерить или оцифровать, но при аудитах интерес сотрудников к работе оценивается количеством предложений о том, что можно улучшить, наличием добровольных групп сотрудников, желающих реализовать какой-нибудь проект.
Также существуют потери, связанные с динамикой протекания процессов, такие как постоянная изменчивость (яп. «мура») или перегрузка (яп. «мури»), транзакционные издержки (связаны с договорной деятельностью, а также менеджментом), недостаточная ценность продукта (несоответствие продукции ожиданиям потребителей).
В качестве упражнения для начинающих изучать бережливое производство рекомендуем составить простую таблицу (см. пример), пройти по предприятию и попытаться обнаружить имеющиеся потери. Потери можно замерить количеством перепроизведенной продукции, временем на устранение брака или пересортицы, длиной дистанции перемещений сотрудников по цехам или временем на транспортировку молока от фермы до завода.
Для проведения самостоятельного аудита очень полезной может оказаться книга известного в России и за рубежом специалиста по применению инструмен тов бережливого производства Майкла Вейдера [3]. Она есть в Интернете и доступна для бесплатного скачивания.
После того как зафиксировано наличие потерь, подсчитайте их в денежном выражении и коллективно подумайте, какими инструментами БП их можно исключить или минимизировать. Если показалось, что потерь нет, следует провести аудит еще раз и посмотреть процессы на всех уровнях создания ценности. Мировой опыт показывает, что лишь 2–5% операций в процессах добавляют ценность, а 95% действий на производстве не добавляют никакой ценности для потребителя. Такие процессы не меняют ни качественные, ни количественные характеристики продукта — в частности, всевозможный контроль, ремонт, транспортировка, хождения, поездки для согласования документов и т.д.
Концепция бережливого производства охватывает все уровни потока создания ценности:
— межорганизационный, когда, например, рассматривается движение потока создания ценности, начиная от аутсорсера (внешняя организация), предоставляющего в аренду молоковозы для доставки молока на завод, и до получения готового продукта клиентом;
— организационный, когда изучаются потери в движении ПСЦ внутри одной организации, например в цехах переработки молока;
— на уровне самих процессов, например приемки молока на заводе;
— на уровне операций, например процесс контроля качества молока на специальном оборудовании.
Руководство должно пристально следить за совершенствованием ПСЦ на каждом уровне, инициировать их постоянное улучшение, информировать сотрудников о предпринимаемых усилиях исключать потери, вовлекать персонал в решение проблем. У руководителей крупных японских компаний слово «кайдзен» (яп. «улучшение») постоянно слетает с языка, и это одна из любимых тем на японских семинарах и тренингах. Кайдзен применим во всех процессах. Поиску возможностей для улучшения руководитель/менеджер/лидер должен посвящать основную долю своего рабочего времени.

Инструменты бережливого производства
Для устранения потерь используются специальные инструменты БП. В ГОСТ Р 56020-2015 в качестве таких инструментов указаны:
— стандартизация работы (standart work). Точное описание каждого действия, включающее время цикла, время такта, последовательность выполнения определенных задач, минимальное количество запасов для выполнения работы;
— организация рабочего пространства (5S). Пять взаимосвязанных принципов организации рабочего пространства, направленных на мотивацию и вовлечение персонала в процесс улучшения продукции, процессов, системы менеджмента организации, снижения потерь, повышения безопасности и удобства в работе;
— картирование потока создания ценности. Карта потока создания ценности (value stream mapping, VSM) представляет собой схему, изображающую каждый этап материального и информационного потока, необходимый для того, чтобы выполнить заказ потребителя;
— визуализация (visualization). Расположение всех инструментов, деталей, производственных стадий и информации о результативности работы производственной системы таким образом, чтобы они были четко видимы и чтобы каждый участник производственного процесса моментально мог оценить состояние системы;
— быстрая переналадка (Single Minute Exchange of Dies, SMED). Процесс переналадки производственного оборудования для перехода от производства одного вида продукта к другому за максимально короткое время;
— защита от непреднамеренных ошибок (poka-yoke). Организационные и инженерные приемы, позволяющие исполнителю при работе избежать ошибок;
— канбан (kanban). Средство информирования, с помощью которого дается разрешение или указание на производство или передачу изделий в производстве, организованном по принципу вытягивания. В переводе с японского «канбан» означает «бирка» или «значок». Наиболее известным и распространенным примером таких средств коммуникации служат карточки канбан. Во многих случаях они представляют собой листки бумаги, иногда помещенные в прозрачные пластиковые конверты, на которых указаны: наименование детали, номер детали, внешний поставщик или внутренний процесс-поставщик, число изделий в упаковке, местоположение склада и процесса-потребителя. На карточке может быть помещен штрихкод для считывания или автоматического выставления счета;
— всеобщее обслуживание оборудования (Total Productive Maintenance, TPM). Система обслуживания оборудования, направленная на повышение эффективности его использования за счет предупреждения и устранения потерь на протяжении всего жизненного цикла оборудования.
К перечисленным в ГОСТ Р 560202015 инструментам мы бы добавили еще несколько:
— вытягивающее производство. Подход к организации потока производства, который исключает потери, связанные с ожиданием, перепроизводством, необходимостью хранить не полуготовую продукцию (semi-fi nished goods). При таком подходе каждая операция технологического процесса как бы «вытягивает» требуемый объем продукта из предыдущей операции и затем передает следующей. Это позволяет избежать как появления излишков продукции, так и ее нехватки;
— система подачи и рассмотрения предложений. Согласно ей, любой сотрудник может предлагать свои идеи по усовершенствованию рабочих процессов. Система включает в себя методы стимулирования сотрудников к предложению своих идей. Этот инструмент тесно связан с непрерывным улучшением качества продукции и процессов, а также с работой малых групп или кружков качества;
— метод «прорыв к потоку», или выравнивание потока. Применяется с целью выровнять и повысить эффективность производственного потока. Для этого создаются фиксированные производственные циклы, в каждый из которых внедряются принципы стандартизированных работ;
— андон. Визуальная система обратной связи;
— производственные ячейки. Расположение оборудования и рабочих мест в такой последовательности, чтобы обеспечить ритмичность потока материалов, комплектующих и прочих компонентов в производственном процессе с минимальными потерями, в частности связанными с задержками на их транспортировку;
— автономизация (autonomization). Передача машине функций человеческого интеллекта. Привнесение человеческого интеллекта в машины предполагает способность оборудования самостоятельно обнаруживать первый дефект, после чего сразу остановиться и сигнализировать о необходимости вмешательства оператора. Этот подход, называемый также «дзидока», впервые был применен в начале XX века Сакити Тоедой в новом проекте автоматического ткацкого станка, который немедленно останавливался при обрыве нити. Благодаря этому оператор мог обслуживать несколько станков при отсутствии бракованной ткани;
— кружки качества. Добровольные и временные объединения сотрудников для совместного решения конкретных проблем с качеством или эффективностью процессов.
Применимость инструментов в разных отраслях промышленности и организациях представлена в таблице.
Для понимания, как применить картирование потока создания ценности (VSM), можем порекомендовать книгу М. Ротера и Д. Шука «Практика построения карт потоков создания ценности. Учитесь видеть бизнес-процессы». Для самого начала рекомендуем прочитать базовую книгу по бережливому производству Д. Вумека и Д. Джонса «Бережливое производство: как избавиться от потерь и добиться процветания вашей компании». Один из крупнейших отечественных специалистов в области бережливых производственных систем, Ю.П. Адлер, призывает руководителей сделать эту книгу настольной и постоянно использовать ее в работе. Также советуем изучать отечественные ГОСТы по бережливому производству. Это ценные источники, устанавливающие единую терминологию и единые подходы к внедрению бережливого производства.
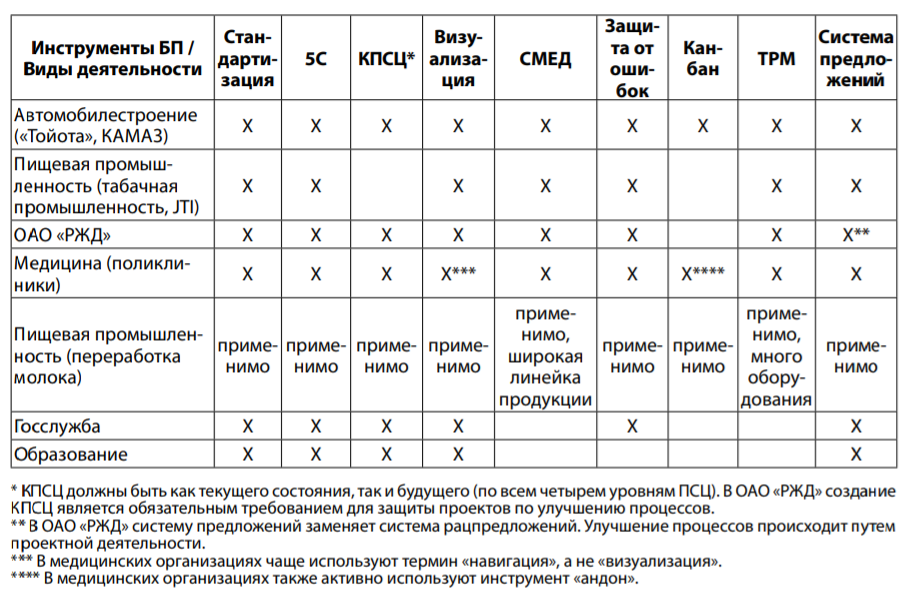
Принципы бережливого производства
Стратегическая направленность. Применение концепции должно быть стратегическим выбором высшего руководства организации.
Ориентация на создание ценности для потребителя. Организация потока создания ценности для потребителя.
Постоянное улучшение.
Вытягивание.
Сокращение потерь. Деятельность по всестороннему сокращению потерь рассматривается как основа улучшения потока создания ценности и снижения затрат. Маржинальная прибыль организации определяется как разница между ценой продукции, формируемой рынком, и себестоимостью, которая формируется на предприятии. Повышение маржинальной прибыли достигается посредством устранения, минимизации потерь, а также посредством создания дополнительной ценности для потребителя.
Визуализация и прозрачность. Управление процессами организации осуществляется таким образом, чтобы все участники процесса могли проследить весь процесс создания ценности и имели необходимую информацию о нем. Это позволяет быстро обнаруживать несоответствия, обеспечивать выполнение стандартов, прозрачность ролей и ответственности работников.
...Неукоснительное соблюдение положений стандартов, регламентов, инструкций и других обязательных документов является необходимым условием функционирования и постоянного улучшения процессов организации...
Приоритетное обеспечение безопасности.
Построение корпоративной культуры на основе уважения к человеку.
Встроенное качество.
Принятие решений, основанных на фактах.
Установление долговременных отношений с поставщиками.
Соблюдение стандартов. Неукоснительное соблюдение положений стандартов, регламентов, инструкций и других обязательных документов является необходимым условием функционирования и постоянного улучшения процессов организации. При выявлении недостатков и/или возможностей их улучшения работники должны следовать указаниям, изложенным в действующих документах до приня тия изменений в установленном порядке.
(Из ГОСТ Р 56020-2014 «Бережливое производство. Основные положения и словарь»)
Продолжение в № 2/2020