В современном машиностроении уже давным-давно стало недостаточно производить просто надежное оборудование для различных, все усложняющихся условий эксплуатации. Сегодня выигрывает тот, кто уделяет должное внимание инновациям, чье оборудование, используемое, например, в добыче, транспортировке и переработке нефти и нефтепродуктов, энергетике, жилищно-коммунальном и водном хозяйстве, химической, угольной, горнодобывающей и металлургической промышленности, отвечает современным требованиям надежности, энергоэффективности, экологической и промышленной безопасности.
Совершенствование процессов и технологий, постоянное повышенное внимание к инновациям в целях улучшения качества производимого оборудования должны являться одними из важнейших ценностей любого высокотехнологичного машиностроительного предприятия.
В современном сельскохозяйственном машиностроении полимерные композиционные материалы с каждым годом получают все большее и большее применение. В основном это связано с тем, что детали подвижных сочленений из металлов (как черных, так и цветных), а также их сплавов не удовлетворяют тем требованиям, которые предъявляются к сельскохозяйственным машинам, в частности к зерноуборочным комбайнам. Эксплуатация последних осуществляется в напряженных режимах: наличие абразива, влаги, температурных колебаний, значительных динамических и знакопеременных нагрузок. Это привело к тому, что традиционные материалы в подвижных сочленениях постепенно стали вытесняться более прогрессивными полимерными композиционными материалами.
Для создания наиболее конкурентоспособной продукции, достижения и удержания лидерства на стратегически приоритетных рынках сегодня могут применяться антифрикционные полимерные композиционные материалы карбонит и оксафен, изделия из которых используются в узлах трения механизмов и агрегатов, эксплуатируемых в средах с высоким содержанием различных абразивов, минеральных масел, нефтепродуктов.
По своим антифрикционным характеристикам данные материалы значительно превосходят по ресурсу и эксплуатационным нагрузкам изделия из баббита, бронзы, текстолита, фторопласта, различных полиамидов (от 2 до 10 раз).
Карбонит — антифрикционный слоистый полимерный конструкционный материал сухого трения, обладающий уникальными трибологическими свойствами для использования в экстремальных условиях сухого трения (низкие и высокие температуры), в различных средах (вода, нефтепродукты и др.), с устойчивостью к истиранию в 5 раз более высокой, чем используемый в настоящее время на многих производствах текстолит (рис. 1, а). Материал включает армирующие полимерные волокна пятого поколения, термостойкое полимерное связующее и функциональные добавки элементоорганическогo строения, а также производные переходных металлов.
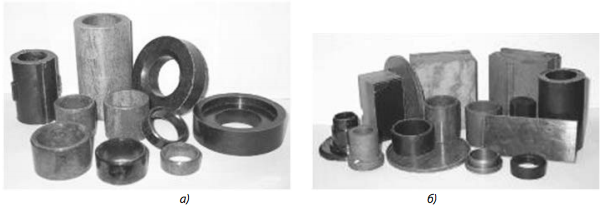
Рис. 1. Примеры деталей, изготовленных из полимеров для отраслей машиностроения
Оксафен — антифрикционный изотропный полимерный конструкционный материал сухого трения. Является следующей ступенью технологического развития материала карбонит, обладает всеми его трибологическими и физико-механическими свойствами. Технология получения материала оксафен позволяет производить сложные изделия необходимой формы на стандартном оборудовании, например тяжело нагруженные втулки транспортных средств, подшипники транспортеров, подшипники скольжения нефтедобывающей техники и многие другие детали (рис. 1, б).
Полимерные композиционные материалы оксафен и карбонит производятся на основе смеси полимерных смол, синтетических волокон полиоксадиазол и целлюлозных волокон. Рецептура материалов запатентована, их свойства детально изучены, отработан технологический процесс получения, научно обоснован и практически отработан режим прессования готовых изделий. Эти материалы являются механически прочными, ударопрочными, термостабильными и износостойкими. Комплекс трибологических свойств данных материалов превосходит аналогичный комплекс свойств черных, цветных металлов, металлокомпозитов, а также большинства используемых в настоящее время полимерных композиционных материалов (различные типы углепластиков, текстолита и др.). Они хорошо поддаются обработке резанием, которое выполняется на обычном металлорежущем оборудовании. Однако скорость резания и скорость подачи, а также инструмент для их обработки должны быть несколько видоизменены ввиду отличия свойств обрабатываемых материалов от свойств металлов. Следует учитывать и температурный режим в зоне резания, так как, помимо пыли, в случае критических перегревов возможны деструкция материала и выделение вредных газообразующих продуктов. В таблице представлены свойства полимерных материалов.
Рассмотрим технологию и способы механической обработки резанием полимерных материалов.
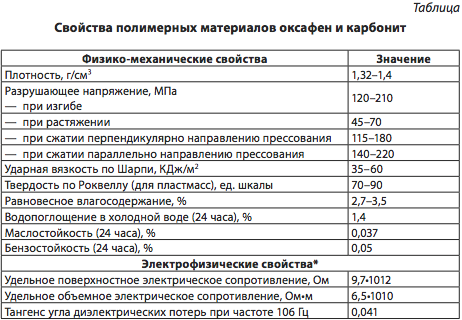
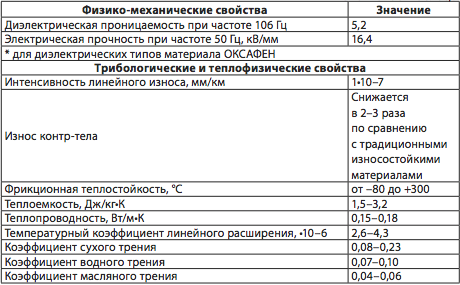
ТОКАРНАЯ ОБРАБОТКА
Токарная обработка деталей из оксафена и карбонита обычно ведется на универсальных металлорежущих станках и токарных автоматах при высоких скоростях резания, но со снятием тонкой стружки. В большинстве случаев охлаждающую жидкость не применяют, однако при обработке материалов допустимая температура в зоне резания не должна превышать 250–300 °С. Следует учитывать, что температура в зоне резания определяется не только скоростью резания, скоростью подачи, глубиной резания, свойствами обрабатываемого материала, но и правильностью и качеством заточки режущего инструмента и свойствами материала режущего клина (рис. 2). Токарные резцы для обработки материалов отличаются от аналогичных для обработки металлов углами заточки.
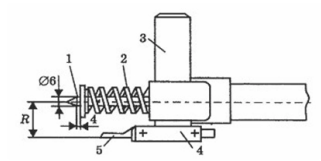
Рис. 2. Циркульный резец: 1 — хвостовик; 2 — пружина; 3 — траверса; 4 — резцедержатель; 5 — резец
ФРЕЗЕРОВАНИЕ
Чаще всего фрезерованием обрабатываются кромки отдельных пластин, листов, деталей из карбонита. Реже фрезерование применяют для дополнительной обработки сложных контуров на уже сформированных деталях из оксафена. Фрезерование осуществляется на обычных горизонтально- или вертикальнофрезерных станках, оснащенных специальными устройствами для улавливания и отсоса стружки и пыли, а также различными зажимными приспособлениями и устройствами. Обработка ведется цилиндрическими или коническими фрезами со специальным спиральным зубом и углом наклона главных режущих кромок к оси фрезы ω = 20–25 град., торцевыми и фасонными фрезами. Фрезы изготавливают из быстрорежущей стали или из твердых сплавов.
К фрезам для обработки полимерных материалов применяются требования:
• меньшее число зубьев (при этом увеличивается объем стружечных канавок);
• большие задние углы;
• простая форма передней поверхности.
Большой угол наклона главных режущих кромок к оси фрезы выполняется с целью обеспечения плавности работы и снижения ударной нагрузки на режущие кромки зубьев.
СВЕРЛЕНИЕ
Сверление может быть как окончательной операцией, так и предварительной перед зенкерованием, развертыванием и нарезанием резьб. В качестве режущих инструментов используют перовые и спиральные сверла из быстрорежущей стали, сверла с твердосплавными пластинами, алмазные сверла, вырезные резцы.
Отверстия большого диаметра в листовом материале могут вырезаться специальным циркульным резцом (рис. 2). Сначала сверлится малое отверстие для фиксирования хвостовика инструмента, а затем производят вырезание отверстия необходимого диаметра.
При сверлении в пластмассах необходимо учитывать сужение отверстий после обработки на 1–2 % вследствие высоких упругих свойств материалов. Соответственно необходимо выбирать сверло большего диаметра. Кроме того, для уменьшения трения ширину направляющей ленточки сверла необходимо делать не более 0,5 мм.
Во избежание выламывания или выкрашивания материала на выходе сквозное сверление нужно производить на гладких прокладках из более мягкого материала, например из древесины. При глубине сверления более 2,5 диаметра отверстия необходимо периодически извлекать сверло из отверстия для удаления стружки и охлаждения. Желательно охлаждение детали производить сжатым воздухом. Для лучшего удаления стружки сверло должно иметь больший угол и широкую стружечную канавку с полированной поверхностью.
РАЗВЕРТЫВАНИЕ
При необходимости получения отверстий с более точными размерами после сверления производится развертывание посредством разверток при скоростях резания 40–90 м/мин с подачей 0,1–0,6 мм/об, при этом рекомендуется под развертку оставлять припуск 0,1–0,2 мм. В таком случае достигается 6–7-й квалитеты точности обрабатываемой поверхности.
Для развертывания используются цилиндрические и конические развертки с прямыми или спиральными зубьями из быстрорежущих сталей с углами заточки γ = 0 град., α = 8 град.
НАРЕЗАНИЕ РЕЗЬБЫ
Получение резьбы в деталях из полимерных материалов возможно двумя путями: без снятия и со снятием стружки.
В первом случае резьба воспроизводится непосредственно при изготовлении детали в форме (однако вследствие усадки пластмасс при отвердении точность такой резьбы невысока). Этот способ применяют для деталей с малонагруженными или неответственными резьбовыми соединениями.
Резьба со снятием стружки оформляется в деталях на металлорежущих станках. Наружную резьбу выполняют резьбонарезными головками, плашками, резцами, резьбовыми гребенками, абразивными кругами, а внутреннюю — метчиками и резцами. Режущий инструмент изготавливают из быстрорежущей стали и твердых сплавов. Твердосплавные метчики применяются с двумя-тремя полированными канавками, несколько более широкими, с передним углом от –10 град. до +10 град. Наружный и средний диаметры метчиков увеличивают на 0,05–0,13 мм.
РАСПИЛИВАНИЕ
Распиливание материалов производится с помощью дисковых, ленточных и циркулярных пил. Выбор конструкции режущего инструмента и режимов резания нужно производить с учетом особенностей заготовки материала.
При заточке зубьев фрез на задних и боковых поверхностях цилиндрические фаски не допускаются. Для обработки нельзя использовать фрезы с большим шагом и малым числом зубьев. В контакте с материалом должны находиться одновременно минимум два зуба, что повышает качество реза и предотвращает сколы материала.
Распиловку тонкого листового материала рекомендуется производить пилами с соответствующей формой пластин из твердого сплава (рис. 3) или из быстрорежущей стали с симметричным зубом и разводом 0,3–0,5 мм на сторону.
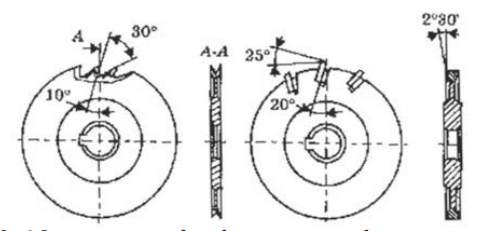
Рис. 3. Дисковые пилы: с разводом зубьев и со вставными зубьями
Для распиловки материалов зубья пил должны быть разведены симметрично в обе стороны. Материал толщиной до 45 мм разрезают дисковыми фрезами из быстрорежущей стали или фрезами, оснащенными твердосплавными пластинами. При распиловке инструментом из быстрорежущей стали рекомендуется выбирать скорости резания 150–400 м/мин и подачи 0,2–0,5 мм/зуб, а твердосплавным инструментом — соответственно 600–1000 м/мин и 0,07–0,3 мм/зуб.
Разрезку производят также корундовыми и алмазными абразивными кругами. Обработку корундовыми кругами толщиной 3–6 мм и диаметром 350 мм следует производить со скоростями резания до 50–60 м/с и подачи 0,01–0,6 м/мин — в зависимости от толщины и направления распиловки относительно армирующих волокон.
Для получения деталей фасонного профиля, резки труб, стержней и других профилей применяют разрезку на ленточных станках. Используют стандартные ленточные пилы (рис. 4) шириной 10–25 мм, толщиной 1,0–1,5 мм с 1,5–5,0 зубьями на 10 мм длины пилы.
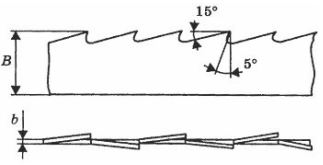
Рис. 4. Ленточное полотно для обработки пластмасс
ШЛИФОВАНИЕ И ПОЛИРОВАНИЕ
Шлифование можно производить на станках, оснащенных специальными дисками, или ручным способом с помощью наждачной шкурки. Используют этот процесс в основном для снятия заусенец с деталей, полученных прессованием, для подготовки деталей к склеиванию, а также для обработки поверхностей, подвергающихся механической обработке, если это требуется по условиям эксплуатации.
Полирование деталей производят с целью устранения с их поверхностей следов предшествующих технологических операций и поверхностных дефектов, полученных в процессе изготовления (например, матовости поверхностей), а также придания им блеска. Полировальные круги изготавливают наборными из тканей (хлопчатобумажной, байковой, суконной). Твердые полировальные круги набираются в шайбы (диаметром 200–400 мм) и толщиной 60–100 мм, зажатые с двух сторон металлическими прокладками. Применяют их для выведения рисок, царапин и других глубоких дефектов.
Окончательное полирование производят мягкими и самоохлаждающимися дисками. Самоохлаждающиеся диски изготавливают путем набора и уплотнения пакета из хлопчатобумажных дисков диаметром 150–300 мм и 40–75 мм, чередуя каждый диск большого диаметра двумя малыми. Толщина пакета обычно составляет 100–120 мм.
Для этих материалов применяют «сухое» полирование. В качестве полировальных паст для сухого полирования используют абразивные компоненты (карборунд, корунд, оксид хрома и др.) в различных соотношениях с воскоабразивными веществами или маслами (парафином, церезином, пчелином воском, машинным, веретенным и другими маслами).
РЕЗУЛЬТАТЫ ИСПЫТАНИЙ И ПРАКТИКИ ПРИМЕНЕНИЯ
Проведенные испытания деталей подвижных соединений зерноуборочных комбайнов из оксафена подтвердили целесообразность применения данного материала в узлах комбайнов, работающих в условиях значительных знакопеременных динамических нагрузок, ограничения или отсутствия смазки, наличия аброзивов и т. д.
Зерноуборочный комбайн (рис. 5) одновременно выполняет несколько функций: скашивание хлебной массы, обмолот, очистку зерна, измельчение соломы, передвижение агрегата с заданной скоростью по полю в процессе работы.
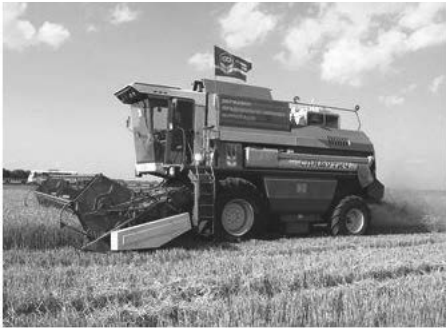
Рис. 5. Общий вид зерноуборочного комбайна
Жатка — первый в технологическом процессе уборки сложный механизм, который «встречает» хлебную массу и предназначен для скашивания (подбора валков) хлебостоя, транспортировки его к центру жатки и подачи сформированной массы в наклонную камеру к молотильному барабану.
Основная нагрузка в данном случае приходится на шнек жатки и глазки (рис. 6), установленные в нем. Этот механизм должен обеспечить своевременную подачу большого количества хлебной массы в наклонную камеру.
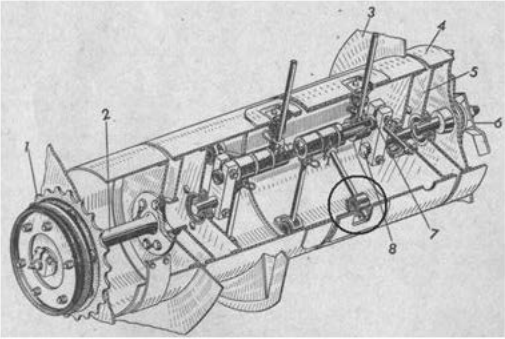
Рис. 6. Шнек жатки комбайна «Дон-1500» (глазок обведен кругом): 1 — приводная звездочка; 2 — ступица; 3 — спиральная лента; 4 — корпус; 5 — диск; 6 — рычаг регулировки пальчикового механизма; 7 — эксцентриковый механизм; 8 — вал управления пальчиковым механизмом
С увеличением пропускной способности комбайна (сегодня она достигает 10–14 кг/с) условия эксплуатации подвижных соединений жатки ужесточаются.
Именно поэтому эксплуатационные характеристики полимерных композиционных материалов, предназначенных для изготовления деталей подвижных соединений зерноуборочных комбайнов, должны отвечать следующим требованиям:
• повышать надежность и долговечность машин;
• увеличивать доремонтный срок службы и продолжительность периодов эксплуатации между техническими обслуживаниями;
• снижать стоимость эксплуатации машин.
Глазки шнека жатки — одни из наиболее часто выходящих со строя деталей зерноуборочных комбайнов (рис. 6). Серийные глазки изготавливаются из металлокерамики, углепластика, множества полимерных материалов, но в любом случае они быстро достигают предельного износа и требуют замены уже через один, реже два сезона работы комбайна.
Глазок работает при давлении 0,45 МПа и максимальной скорости скольжения пальца по его поверхности 0,4–0,45 м/с. Деталь работает в режиме сухого абразивного изнашивания в присутствии почвы, зернового и соломистого вороха, растительных остатков. Смазка отсутствует.
Экспериментальные глазки шнека жатки изготавливали из оксафена методом прямого компрессионного прессования. Детали были переданы на полевые испытания и установлены на зерноуборочный комбайн «Дон-1500». Наработка комбайна, укомплектованного экспериментальными деталями, на уборке ранних зерновых колосовых культур составила 164 га, при намолоте зерна 538 т.
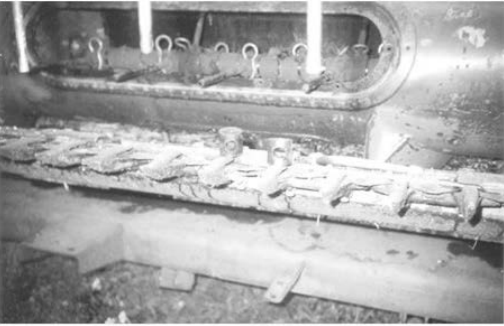
Рис. 7. Пальчиковый механизм шнека жатки в разобранном виде при проведении микрометража
Микрометраж глазков производился в конце уборочной кампании (рис. 7) совместно специалистами Днепропетровского государственного аграрного университета и инженернотехнической службой предприятия, в процессе которого было установлено следующее:
• на протяжении наработки комбайна 164 га глазки отличались высокой надежностью в работе;
• выхода из строя или поломок, других нежелательных явлений в процессе эксплуатации экспериментальных глазков не наблюдалось;
• глазки находятся в работоспособном состоянии, по результатам испытаний замечаний нет;
• износ глазков в среднем составляет 22–23 % от предельно допустимого, и они рекомендованы к дальнейшим испытаниям.
Как видно из результатов микрометража, износ глазков колеблется в пределах от 0,37 до 0,56 мм, что можно объяснить неравномерной подачей хлебной массы к центру шнека жатки, следовательно нагрузка на каждый глазок будет разной и износ неравномерным. Однако даже при максимально зафиксированном значении износ (всего лишь у одного глазка) составляет немногим более 25 % от предельно допустимого износа, равного 2,0 мм. Исходя из этого, можно сделать заключение, что ресурс экспериментальных глазков должен быть не ниже 4 уборочных сезонов при сезонной наработке комбайна 160–170 га.
Скребки зерновых элеваторов (рис. 8) предназначены для транспортировки зерна и зерносмесей в различных плоскостях и применяются как в зерноуборочных комбайнах, так и в зерносушильных комплексах. При этом нагрузка на элеваторы в зерносушильных комплексах намного больше, чем в зерноуборочных комбайнах, так как работают они практически круглый год. Производственные испытания экспериментальных скребков на зерносушильном комплексе Pektus (Германия) показали их преимущества по сравнению с серийными. Уже через 5120 ч раб оты у серийных скребков появились дефекты формы и заметный износ рабочих поверхностей, чего не было у экспериментальных скребков. Скребки оставлены для дальнейших испытаний.
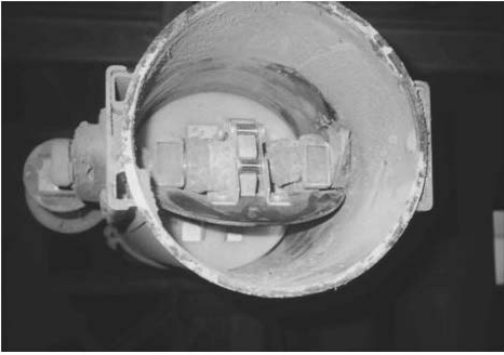
Рис. 8. Фрагмент зернового элеватора фирмы Pektus
Необходимо отметить, что в настоящий момент успешно завершены испытания антифрикционных полимерных композиционных материалов оксафен и карбонит на машиностроительных предприятиях и они уже сейчас применяются:
• в погружных насосных установках типа УЭЦН;
• на городском пассажирском транспорте — втулки шкворней поворотных цапф подвески троллейбусов и автобусов;
• в компрессорной технике — лопатки вихревых компрессорных станций цементного производства;
• в лесоперерабатывающей промышленности — ползуны направляющих пилорам.
ЗАКЛЮЧЕНИЕ
Многолетняя эксплуатация изделий в высоконагруженных узлах трения всевозможных агрегатов, работающих в самых различных условиях эксплуатации, доказала, что использование износостойких композиционных материалов позволяет значительно увеличить ресурс механизмов, повысить их надежность за счет низкого коэффициента трения, снизить затраты при ремонте и эксплуатации. Применение антифрикционных полимерных композиционных материалов карбонит и оксафен позволяет снизить количество внеплановых простоев оборудования и, как следствие, обеспечить снижение расходов на его ремонт и обслуживание.