ВВЕДЕНИЕ
В современной промышленности порошковая металлургия представляет собой инновационную технологию изготовления металлических изделий, основанную на процессах формирования и спекания металлических порошков. Данный метод обеспечивает высокую точность производства при минимизации отходов, что обуславливает его широкое применение в автомобилестроении, аэрокосмической отрасли и медицинской промышленности. Развитие зарубежного производства железных порошков характеризуется следующими ключевыми тенденциями: увеличение объемов выпуска и значительное улучшение качества массово производимых порошков, обеспечение стабильности состава и свойств материалов, внедрение сертификации продукции, освоение производства высокочистых распыленных порошков с улучшенной уплотняемостью, расширение ассортимента легированных порошков на основе высококачественного железа, производство готовых к прессованию порошковых смесей с улучшенными характеристиками текучести и устойчивостью к сегрегации.
Согласно данным Международной конференции PM TEC 99 и отраслевого семинара 1999 г., мировой рынок изделий порошковой металлургии демонстрирует устойчивый рост. Прогнозируемый ежегодный прирост составляет 8…12%, с ожидаемым объемом продаж 15…18 млрд долл. США к 2025 г. При этом 85% мирового производства базируется на использовании железных, железомедных и стальных порошков.
Технологический процесс порошковой металлургии включает четыре основных этапа производства.
Первый этап — получение металлических порошков реализуется несколькими способами. При атомизации расплавленный металл распыляется в мелкие капли, которые затвердевают в порошок. Различают газовую атомизацию с использованием инертных газов, водную атомизацию и центробежное распыление. Химическое восстановление позволяет получать высокочистые порошки путем обработки оксидов металлов реагентами. Электролитический метод основан на электролизе растворов или расплавов солей и особенно эффективен для меди и никеля. Механическое измельчение применяют для твердых и хрупких материалов с использованием мельниц или вальцов.
Второй этап включает формирование заготовок путем прессования порошковых смесей. При одноосном прессовании порошок сжимается в форме в одном направлении, что подходит для простых деталей. Изостатическое прессование обеспечивает равномерное всестороннее сжатие в гибком контейнере, позволяя создавать сложные формы. Также применяется метод литья, где порошок смешивается со связующим веществом.
На третьем этапе происходит спекание — нагрев заготовок до температуры ниже точки плавления. Этот процесс обеспечивает сплавление частиц, повышает прочность, снижает пористость и позволяет контролировать микроструктуру материала путем регулирования температурно-временных параметров.
Заключительный этап — механическая обработка для достижения требуемых размеров и качества поверхности, а также термическая обработка для улучшения механических характеристик изделий.
ТЕХНОЛОГИИ В ПОРОШКОВОЙ МЕТАЛЛУРГИИ
Революционным прорывом в развитии порошковой металлургии стало освоение аддитивных технологий, в частности селективного лазерного плавления (SLM) и электронно-лучевого плавления (EBM) (рис. 1). Данные методы, основанные на использовании направленных источников энергии — лазерного луча или электронного пучка, в сочетании с металлическими порошками позволяют изготавливать изделия со сложной геометрической конфигурацией [1–5].
В технологии аддитивного производства селективное лазерное плавление (SLM) занимает лидирующие позиции. Метод основан на послойном формировании изделия путем равномерного нанесения металлического порошка на рабочую поверхность с последующим локальным расплавлением материала лазерным лучом в заданных областях каждого слоя (рис. 1).
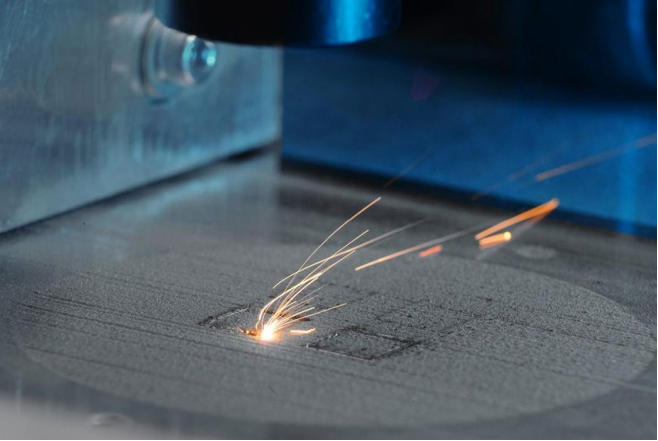
Рис. 1. Пример селективного лазерного плавления (SLM)
Технология SLM обладает рядом существенных преимуществ: обеспечива ет изготовление деталей с микронной точностью, позволяет создавать изделия со сложной геометрией, включая внутренние полости и каналы, недостижимые при традиционных методах обработки, а также характеризуется широкими возможностями использования различных металлических материалов — от титановых и алюминиевых сплавов до коррозионностойких сталей [2].
В технологии электронно-лучевого плавления (EBM) для расплавления металлического порошка применяют электронный пучок. Как и в других аддитивных технологиях, процесс построения изделия происходит послойно, однако использование электронного пучка вместо лазерного излучения обеспечивает достижение более высоких температур обработки.
К основным достоинствам технологии EBM относятся:
• возможность обработки тугоплавких материалов, в частности никелевых суперсплавов, благодаря высоким рабочим температурам;
• повышенная производительность процесса по сравнению с SLM за счет более мощного энергетического воздействия;
• минимизация остаточных напряжений в готовых изделиях благодаря более равномерным условиям нагрева и охлаждения материала.
Селективное лазерное спекание (SLS) представляет собой технологию, в которой лазерное излучение используется для частичного спекания порошковых материалов без их полного расплавления. Данный метод эффективен при работе с материалами, имеющими относительно низкую температуру плавления [3].
Технология SLS обладает рядом преимущественных характеристик:
• универсальность применения для различных материалов (металлы, полимеры, композиты);
• экономическая эффективность при мелкосерийном производстве в сравнении с технологиями SLM и EBM;
• обеспечение механических свойств, удовлетворяющих требованиям большинства практических применений.
Аддитивное производство обеспечивает беспрецедентную гибкость в проектировании изделий. В отличие от традиционных технологий (литья, ковки, механообработки), которые имеют существенные ограничения по форме, 3D-печать позволяет создавать изделия практически любой геометрической сложности, включая внутренние полости и криволинейные поверхности.
В противоположность традиционным методам обработки, требующим удаления значительного объема материала, аддитивные технологии реализуют принцип построения изделия путем добавления материала исключительно на требуемых участках. Это обеспечивает существенное снижение отходов производства, повышая его экологичность и экономическую эффективность [4].
Аддитивные технологии обеспечивают эффективное производство индивидуализированных изделий, что особенно актуально в медицинской отрасли при изготовлении имплантатов и протезов, а также в других сферах, требующих кастомизации продукции.
Применение аддитивных технологий значительно сокращает цикл разработки изделий, позволяя оперативно создавать и тестировать прототипы. Это обеспечивает ускоренный вывод продукции на рынок и повышение эффективности процесса разработки. Отраслевое применение аддитивных технологий, например в авиационной промышленности, эффективно для производства облегченных конструкций, включая топливные форсунки и элементы двигателей, что способствует снижению веса летательных аппаратов и повышению их топливной эффективности.
Аддитивные технологии используют для изготовления прототипов, компонентов двигателей и элементов кузова, что ускоряет процессы разработки и тестирования новых моделей для автомобилей, авиационной и космической промышленности. В медицине аддитивные технологии обеспечивают производство персонализированных имплантатов, ортопедических изделий и протезов, точно соответствующих анатомическим особенностям пациентов, что повышает эффективность лечения и уровень комфорта.
МЕТАЛЛУРГИЯ ПОРОШКОВ С НАНОЧАСТИЦАМИ
Порошковая металлургия с применением наноразмерных частиц обеспечивает улучшенные характеристики материалов благодаря использованию металлических частиц нанометрового масштаба (рис. 2). Уникальные физикохимические свойства наночастиц существенно расширяют технологические возможности традиционной порошковой металлургии. Рассмотрим фундаментальные аспекты, технологические особенности, преимущества и области практического применения нанопорошковой металлургии.
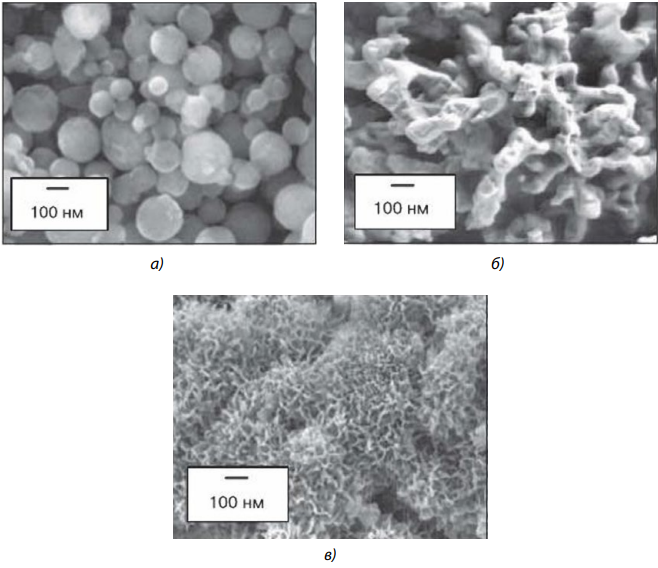
Рис. 2. Использование металлических частиц нанометрового масштаба: а–в — примеры наноразмерных частиц
Нанопорошковая металлургия основана на введении наноразмерных частиц (размером менее 100 нм) в металлические порошковые композиции на этапе, предшествующем спеканию. Высокое значение удельной поверхности наночастиц обеспечивает интенсификацию процессов спекания и, как следствие, улучшение эксплуатационных характеристик получаемых материалов [1–3].
Основными преимуществами использования наночастиц в порошковой металлургии являются:
• достижение повышенных показателей прочности материала благодаря эффектам блокировки дислокаций и зернограничного упрочнения;
• значительное увеличение твердости вследствие формирования более прочных межчастичных связей, обусловленных высокой удельной поверхностью наночастиц;
• существенное повышение износостойкости за счет образования более плотной и однородной структуры материала;
• улучшенная термическая стабильность, характеризующаяся повышенной температурой плавления и пониженной теплопроводностью наноструктурированных материалов.
Технология получения наночастиц для их последующего применения в порошковой металлургии реализуется различными методами.
Химическое восстановление основано на восстановлении металлов из растворов солей, чем обеспечивается возможность контроля морфологии и размеров получаемых наночастиц при достижении их высокой чистоты. При электролитическом синтезе происходит осаждение наночастиц из растворов металлических солей в строго контролируемых условиях, что гарантирует получение высококачественного продукта. Механическое диспергирование предусматривает измельчение металлических материалов до наноразмерного состояния с использованием высокоэнергетического размольного оборудования, что позволяет получать наночастицы различных металлов и их сплавов.
Сферы промышленного использования нанопорошковых технологий достаточно широкие. Например, в авиакосмическом комплексе внедрение наноматериалов позволяет разрабатывать легковесные конструкции из алюминиевых и титановых композиций, гарантирующие стабильную работу изделий при воздействии экстремальных эксплуатационных факторов. В автомобильной индустрии применение наноструктурированных материалов обеспечивает улучшение рабочих параметров элементов двигателей и рулевых систем, существенно повышая их долговечность и стойкость к износу [5]. В медицинской сфере наноматериалы на основе оксида титана и кобальт-хромовых сплавов успешно применяют в производстве медицинских имплантатов и протезов, демонстрируя оптимальное сочетание биологической совместимости и прочностных характеристик. Электронная и энергетическая отрасли активно используют нанотехнологии при создании эффективных проводников и полупроводников, а также для оптимизации рабочих параметров аккумуляторных систем и топливных элементов.
Рассмотрим один из технологических методов получения заготовок и готовых деталей из порошков.
ГОРЯЧЕЕ ИЗОСТАТИЧЕСКОЕ ПРЕССОВАНИЕ (HIP) В ПОРОШКОВОЙ МЕТАЛЛУРГИИ
Технология горячего изостатического прессования (HIP) представляет собой ключевой метод порошковой металлургии, обеспечивающий получение высокоплотных изделий с улучшенными механическими характеристиками. Процесс основан на одновременном воздействии высоких давлений и температур при спекании порошковых материалов, что позволяет практически полностью устранить пористость и достичь максимальной плотности материала. Оборудование для HIP представлена на рис. 3. Далее будут рассмотрены основные принципы реализации процесса, технологические этапы, преимущества метода и области его промышленного применения.
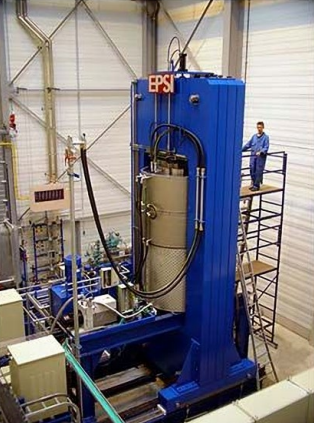
Рис. 3. Оборудование для горячего изостатического прессования
Технология горячего изостатического прессования основана на всестороннем изостатическом воздействии давления на заготовку при повышенных температурах. В ходе процесса HIP образец из порошкового материала размещается в специальном герметичном контейнере, где подвергается воздействию инертного газа (преимущественно аргона) в условиях высокого давления и температуры [2–5].
Ключевые технологические параметры HIP-процесса:
1. Температурный режим: определяется свойствами обрабатываемого материала и находится в интервале 900–1250 °C.
2. Давление прессования: регулируется в диапазоне от 100 до 200 Мпа.
3. Продолжительность процесса: варьируется от нескольких минут до нескольких часов в зависимости от габаритных размеров заготовки и характеристик материала.
Технологический процесс HIP включает следующие этапы:
• формирование заготовки осуществляется методом холодного изостатического прессования (CIP) или иными способами предварительного прессования. Подготовленная заготовка помещается в герметичный металлический или стеклянный контейнер, обеспечивающий защиту от внешней среды и равномерное распределение давления;
• сформированная заготовка загружается в автоклав установки HIP, оснащенный системами нагрева и создания высокого давления (рис. 3). Рабочей средой служит инертный газ (аргон), предотвращающий химическое взаимодействие с порошковым материалом;
• на данном этапе происходит синхронное воздействие высоких температур и давлений, обеспечивающее спекание частиц порошка и уплотнение материала. Параметры процесса контролируются для создания оптимальных условий спекания;
• по завершении процесса производится постепенное снижение температуры и давления до значений 20…30 0С. После охлаждения заготовка извлекается из установки и при необходимости освобождается от контейнера.
Применение метода обеспечивает полную ликвидацию пористости и достижение максимальной плотности материала, что особенно важно при производстве ответственных конструкций, где предъявляются повышенные требования к механическим характеристикам и надежности изделий. Обработка методом HIP обеспечивает существенное улучшение комплекса механических свойств материала (прочности, твердости, износостойкости) благодаря формированию плотной структуры и минимизации внутренних дефектов. Метод гарантирует равномерное распределение физико-механических свойств по всему объему изделия, что особенно важно при производстве крупногабаритных и геометрически сложных компонентов, требующих стабильности характеристик. Технология позволяет обрабатывать изделия сложной конфигурации, включая детали с внутренними полостями, что делает метод уникальным для производства компонентов, изготовление которых затруднено или невозможно другими способами [3].
Метод HIP применяют при производстве компонентов авиационной и космической техники — лопаток турбин, дисков и других элементов двигательных установок. Достигаемые высокие показатели прочности и надежности материалов обеспечивают требуемый уровень безопасности и ресурса летательных аппаратов. В медицинской промышленности технологию используют для изготовления имплантатов и хирургического инструментария из титана и кобальт-хромовых сплавов. В автомобилестроении метод HIP внедрен в производство высоконагруженных деталей силовых агрегатов и трансмиссий, где повышенные показатели прочности и износостойкости материалов способствуют увеличению ресурса техники и снижению эксплуатационных расходов. В энергетике технологию применяют при изготовлении компонентов газовых и паровых турбин, а также элементов ядерных установок, где высокая плотность и механические характеристики материалов обеспечивают надежную работу оборудования в экстремальных условиях.
ИННОВАЦИОННЫЕ СПЛАВЫ И МАТЕРИАЛЫ В ПОРОШКОВОЙ МЕТАЛЛУРГИИ
В современном материаловедении порошковая металлургия занимает позицию одного из наиболее интенсивно развивающихся направлений. Данная технология предоставляет широкие возможности для разработки передовых сплавов и материалов с улучшенными эксплуатационными характеристиками. В последующем материале будут рассмотрены современные достижения и инновационные разработки в области порошковой металлургии, включая новые сплавы, композиционные материалы и наноструктурированные системы [4].
Высокоэнтропийные сплавы (HEAs). В области современной металлургии HEAs являются новым классом материалов, в составе которых содержится пять или более химических элементов в эквивалентных или близких к эквивалентным соотношениях. В отличие от традиционных металлических систем, базирующихся на одном-двух основных компонентах, высокоэнтропийные сплавы демонстрируют уникальные структурные особенности и комплекс свойств, обусловленные повышенной энтропией смешения. Преимущества HEAs: повышенные показатели прочности и твердости, обусловленные комплексной микроструктурой и гомогенным распределением элементов, термическая стабильность, проявляющаяся в сохранении механических характеристик при воздействии высоких температур, высокая устойчивость к процессам окисления и коррозионным воздействиям, улучшенная сопротивляемость износу, определяющая перспективность применения материалов в условиях экстремальных нагрузок [3].
Аморфные металлы (Bulk Metallic Glasses, BMGs). Аморфные металлические сплавы (металлические стекла) формируются в процессе сверхбыстрого охлаждения, препятствующего образованию кристаллической структуры и обеспечивающего формирование аморфного состояния. Эти материалы характеризуются комплексом уникальных свойств, существенно отличающих их от кристаллических аналогов. Из преимуществ можно отметить: сверхвысокие прочностные характеристики, превосходящие показатели традиционных кристаллических материалов, повышенная способность к упругой деформации без разрушения структуры, исключительная стойкость к воздействию коррозионных сред и процессам окисления, особые магнитные характеристики отдельных составов, определяющие их перспективность для электронных изделий [2].
Композиты на основе металлических матриц (MMCs). Металлические композиционные материалы (MMCs) представляют собой системы, состоящие из металлической матрицы, армированной неметаллическими компонентами (керамикой, углеродными волокнами). Такая комбинация позволяет получать материалы с уникальным сочетанием свойств, недостижимым для монометаллических систем и традиционных сплавов. Основные достоинства металлических композитов: усиленные механические характеристики (прочность, жесткость), обеспечиваемые введением армирующих наполнителей, высокая термическая стабильность, определяющая возможность применения материалов в двигательных установках и турбинных агрегатах, повышенная сопротивляемость износу, критичная для узлов трения, сниженная плотность отдельных композиций, достигаемая введением легких наполнителей, что особенно важно для авиакосмической техники.
Наноструктурированные материалы. Внедрение нанотехнологий в порошковую металлургию обеспечивает получение материалов с наноструктурированным строением, определяющим их особые механические, термические и электрические характеристики.
Наноструктурированные материалы характеризуются следующими преимуществами: значительное повышение механической прочности за счет формирования мелкозернистой структуры и высокого отношения площади поверхности к объему, существенное увеличение твердости, обусловленное повышенным сопротивлением пластическому деформированию, возможность регулирования электропроводящих свойств материалов, управляемое изменение теплофизических характеристик (повышение или снижение теплопроводности) в зависимости от требований конкретного применения.
Интерметаллиды. Соединения двух или более металлов, образующие интерметаллиды, характеризуются формированием упорядоченных фаз с особым комплексом свойств. Данные материалы эффективно применяются в условиях воздействия высоких температур и агрессивных сред благодаря их исключительной стойкости и механическим свойствам [1, 3].
Ключевыми преимуществами интерметаллидных соединений являются: высокая термостойкость благодаря высоким температурам плавления, обеспечивающая возможность применения в турбинных установках и двигательных агрегатах, устойчивость к воздействию агрессивных химических сред, сохранение высоких показателей прочности и жесткости при повышенных температурах эксплуатации.
Легкие, прочные и термостойкие высокоэнтропийные сплавы, композиты и наноструктурированные материалы активно внедряются в производство компонентов двигательных установок, элементов конструкций и теплообменных систем авиакосмической техники. Новые материалы используют в производстве облегченных компонентов двигателей, элементов кузова и выхлопных систем. Особую роль играют композиты на основе алюминия и магния, обеспечивающие снижение массы транспортных средств и, как следствие, повышение топливной эффективности и сокращение вредных выбросов. Жаропрочные интерметаллиды и наноструктурированные сплавы применяют при изготовлении турбинных компонентов, теплообменного оборудования и других элементов энергетических установок, обеспечивая их надежное функционирование в условиях экстремальных температур и давлений. Аморфные и наноструктурированные материалы находят применение в производстве биосовместимых имплантатов и медицинского инструментария благодаря высокой прочности, коррозионной стойкости и возможности адаптации свойств под конкретные медицинские задачи [1, 3–5].
ЗАКЛЮЧЕНИЕ
Развитие порошковой металлургии характеризуется непрерывным совершенствованием технологических процессов и разработкой новых материалов. Внедрение аддитивных технологий, применение наноразмерных компонентов, освоение методов горячего изостатического прессования и создание инновационных сплавов существенно расширяют возможности получения изделий с уникальным комплексом свойств. Эти достижения не только оптимизируют существующие производственные процессы, но и открывают новые перспективы применения порошковой металлургии в различных промышленных секторах.